Blog
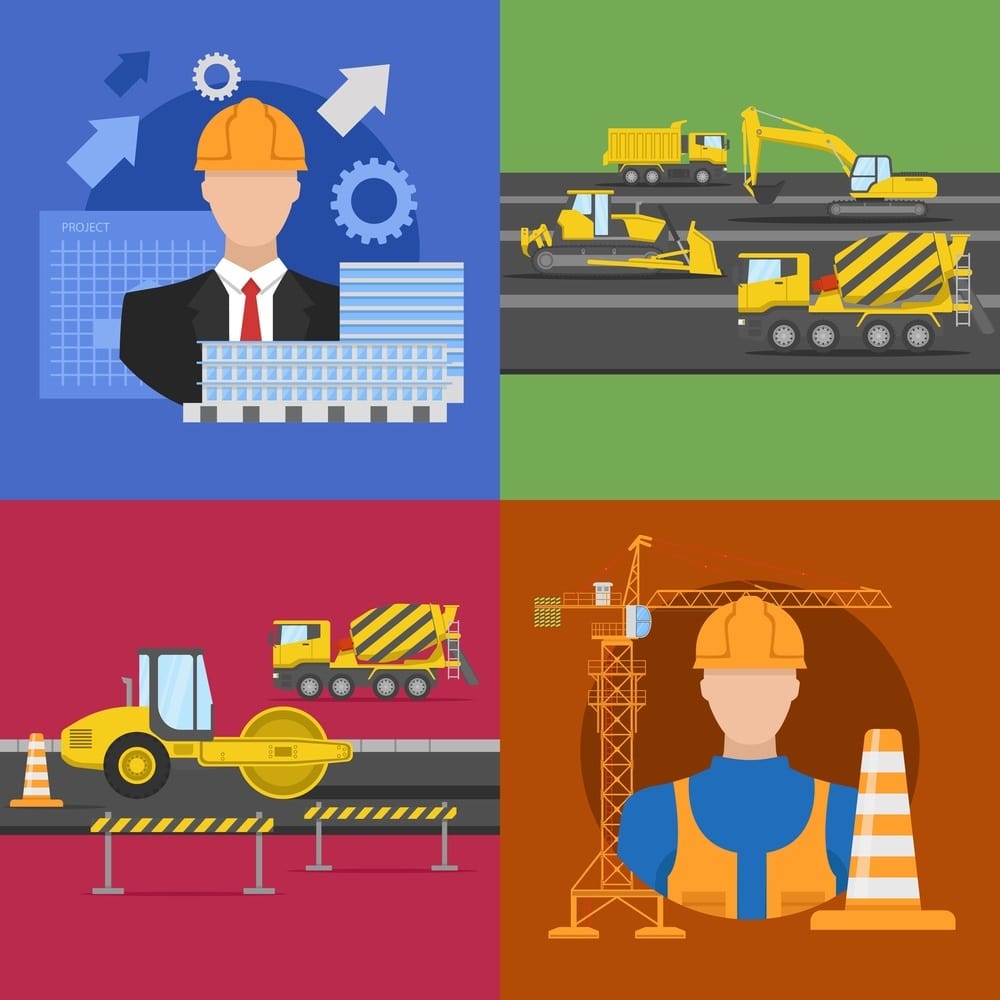
Płyty wiórkowo-cementowe uprawnienia budowlane
W artykule znajdziesz:
Płyty wiórkowo-cementowe uprawnienia budowlane

Do produkcji płyt stosowane są wiórki drzewne (znane pod nazwą wełny drzewnej) produkowane w zasadzie z nienadających się do przeróbki tartacznej części drewna iglastego, zdrowych, dostatecznie wysuszonych (przynajmniej po kilku miesiącach od ścięcia) (program uprawnienia budowlane na komputer).
Bardziej wskazane jest drewno o umiarkowanej ilości żywicy, jak jodła, aniżeli drewno silnie żywiczne, jak sosna. Drewno drzew liściastych nie nadaje się do powyższego celu. Norma PN-54/B-20101 zaleca stosowanie wiórków o długości 200-500 mm. Ilość wiórków o długości poniżej 200 mm nie może przekraczać 20%. Szerokość wiórków 4-6 mm. Maksymalna ilość wiórków cieńszych lub grubszych nie może być większa niż 10%. Niedopuszczalne są wiórki wykazujące oznaki murszu miękkiego, natomiast sinizna i nienormalne zabarwienie nie są brane pod uwagę (program uprawnienia budowlane na ANDROID).
Wilgotność wiórków nie może przekraczać 22% w stosunku do stanu zupełnie suchego. Do wiórków wełny drzewnej można dodawać strużkę stanowiącą odpady z maszyn stolarskich. Ilość tego dodatku może wynosić około 65% w stosunku do ciężaru wełny drzewnej. Ponieważ wełna drzewna jest produktem kosztownym, a strużka odpadem, przeto zastosowanie jej w znacznym procencie obniża koszt płyt. Strużka wpływa na zagęszczenie struktury płyt, należy jednak mieć na uwadze, że dodawanie strużki powoduje pogorszenie izolacji cieplnej płyt.
spoiwem płyt jest cement portlandzki. Niektóre wytwórnie stosują z powodzeniem cement hutniczy. Jeśli chodzi o szybsze twardnienie płyt, a zatem o krótsze przetrzymywanie ich w formach (lepsze wykorzystanie form), wskazane jest stosowanie cementu marki 350. W produkcji płyt rozróżnia się 5 zasadniczych czynności: mineralizację, mieszanie, formowanie, prasowanie i dojrzewanie.
Mineralizacja. Przy produkcji płyt z lepiszczem cementowym wiórki przed wymieszaniem z cementem poddaje się procesowi mineralizacyjnemu (uprawnienia budowlane). Celem mineralizacji jest:
a) zabezpieczenie wiórków od gnicia,
b) zmniejszenie zmian objętościowych przy wysychaniu i nawilżaniu,
c) powiększenie przyczepności wiórków do cementu.
środek mineralizacyjny stosuje się przede wszystkim roztwór chlorku wapnia (program egzamin ustny).
Okres procesu mineralizacyjnego
Okres procesu mineralizacyjnego nie może być zbyt długi, aby nie dopuścić do występowania ujemnych skutków przesadnej mineralizacji, a przede wszystkim do znaczniejszego zmniejszenia plastyczności włókien drzewnych.
Mineralizacja polega na moczeniu wełny drzewnej i ewentualnie strużki w basenach betonowych. W nowoczesnych zakładach produkcyjnych stosuje się natryskiwanie wełny roztworem mineralizatora.
Mieszanie. Mieszanie zmineralizowanej wełny z cementem odbywa się w mieszarkach w postaci bębnów walcowych o pojemności około 1 m: Najlepsze wyniki otrzymuje się w bębnach o ruchu ciągłym. Bęben tak: ma średnicę co najmniej 2 m, a długość 6-ę-8 m. Jest on lekko pochyły, wewnątrz ma pręty ze stali sprężystej. Pręty te ułatwiają dokładne otoczenie każdego wiórka wełny cementem.
powinno się odbywać tak długo, aby włókna otoczone były dokładnie zaczynem cementowym, to znaczy, aby nie prześwitywały surowe powierzchnie włókien. Zaczyn cementowy powinien utrzymywać się na włóknach i nie spływać przy przewożeniu lub przenoszeniu masy na miejsce formowania płyt lub w czasie formowania.
Formowanie. Formy do płyt, wykonane z drewna lub metalu, umieszczone są na stole rolkowym pod mieszarką (opinie o programie). Stół rolkowy stoi na wadze, która automatycznie reguluje ilość mieszaniny potrzebnej na płyty o określonych wymiarach. Po napełnieniu form wyrównuje się nasypaną mieszaninę, a następnie formy przesuwa się do prasy.
Prasowanie. W prasie umieszczone są formy na specjalnym stojaku. Przy grubości płyt 5 cm jednocześnie prasuje się 15 płyt, a przy grubości 7 cm - 12 płyt. Ciśnienie robocze wynosi do 150 at n, wydajność prasy - do 100 sztuk płyt na godzinę.
Sprasowane w formach płyty przewozi się na wózkach do suszarni urządzonej podobnie jak suszarnia drewna. Płyty przebywają tam w temperaturze 65-70°C w ciągu 3 do 5 godzin. Po tym czasie, gdy nastąpi związanie cementu, można już wyjąć płyty z form i ułożyć je jedna na drugiej, tak aby przez pewien czas nie traciły ciepła (segregator aktów prawnych). Po 48 godzinach płyty przenosi się na stosy przewiewne, chronione od działania słońca i opadów atmosferycznych. Stosy powinny być ustawiane na dokładnie wyrównanym podłożu, aby nie dopuścić do zwichrowania płyt.
nadają się do przewożenia; w lecie po około 3 tygodniach a w czasie chłodniejszym po około 4 tygodniach. Ponieważ skurcz płyt wiórkowo-cementowych podobnie jak i betonów z wypełniaczami organicznymi jest szczególnie duży w porównaniu z wyrobami betonowymi z kruszywem mineralnym, przeto nie należy przed upływem około 6 tygodni od sprasowania płyt, tj. przed zakończeniem okresu największego kurczenia się, używać ich do tych części budowli, w których ten skurcz może być szkodliwy.
powyższe jak również zjawisko skurczu można dość znacznie zredukować przez zastosowanie dojrzewania w parze niskoprężnej z jednoczesnym stopniowym podgrzewaniem do około 80°C (około 2 godzin a następnie utrzymaniem tej temperatury w czasie około 4 godzin i powolnym ostudzeniem po wyjęciu z form (około 8 godzin).
Tak potraktowane płyty po dalszym składowaniu w szopie w ciągu 3 dni mogą uzyskać wytrzymałość 28-dniową płyt dojrzewających w zwykły sposób (promocja 3 w 1).
Najnowsze wpisy
W ostatnich latach rozwój sztucznej inteligencji (SI) gwałtownie przyspieszył, wkraczając niemal w każdą dziedzinę naszej codzienności. Nie inaczej jest w…
Rosnąca potrzeba przyspieszenia procesów budowlanych, ograniczenia kosztów i minimalizacji negatywnego wpływu branży na środowisko sprawia, że innowacyjne technologie przyciągają coraz…
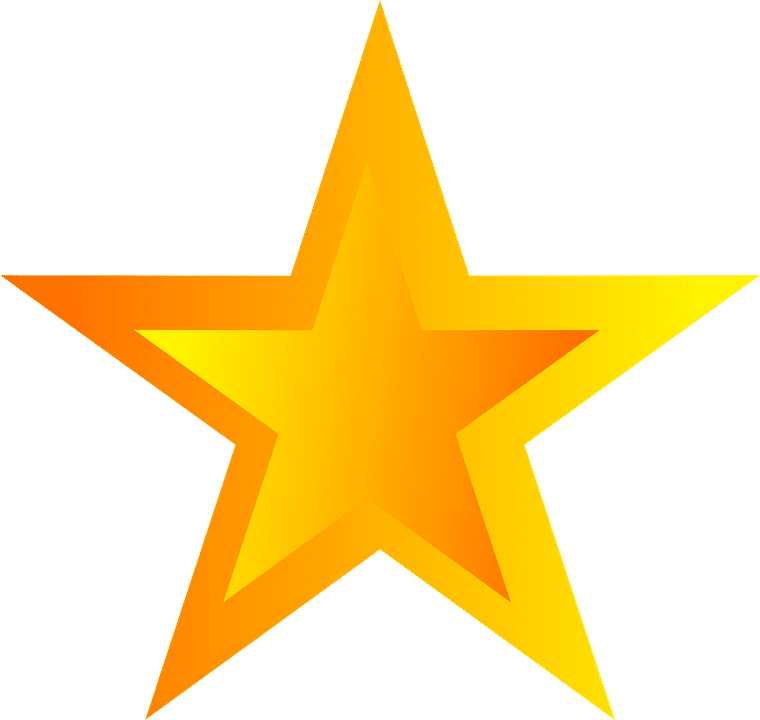
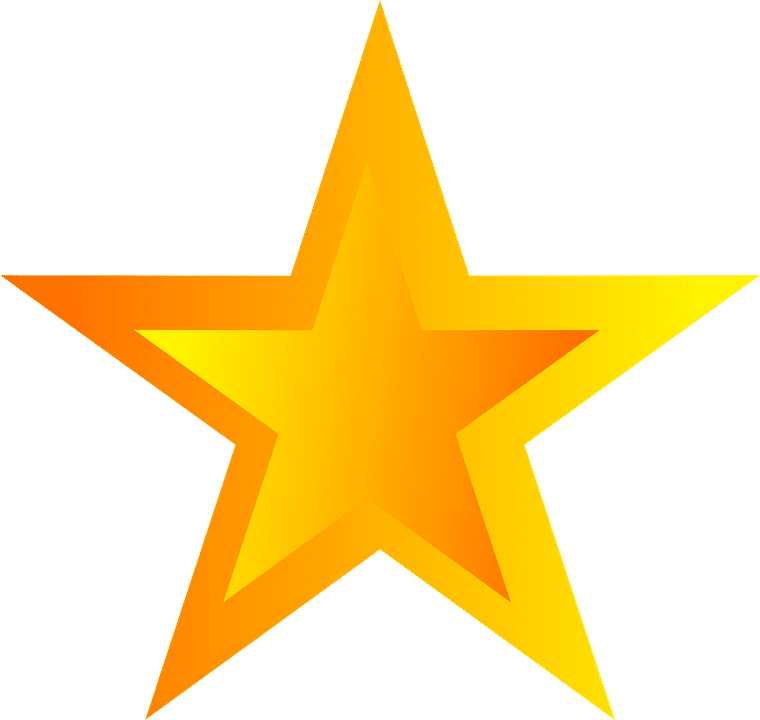
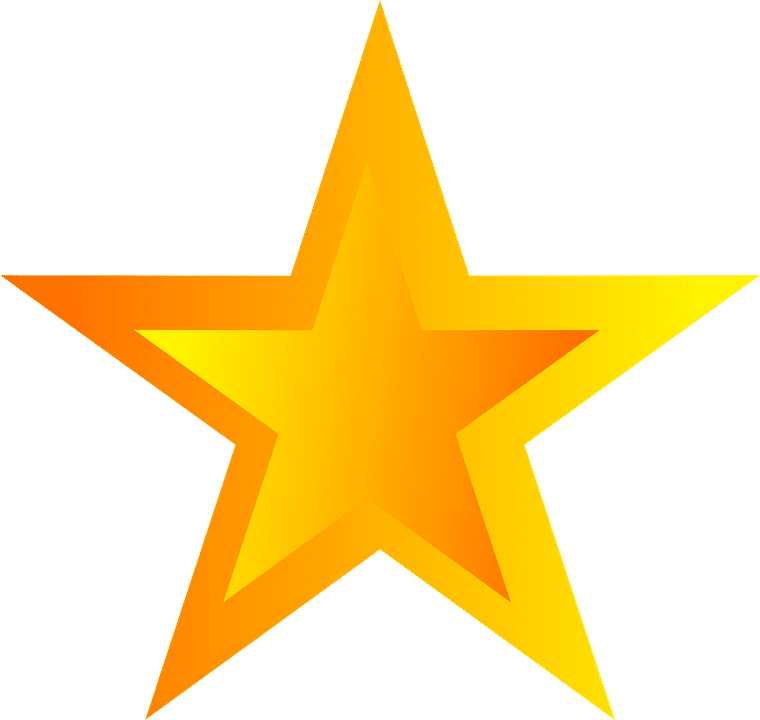
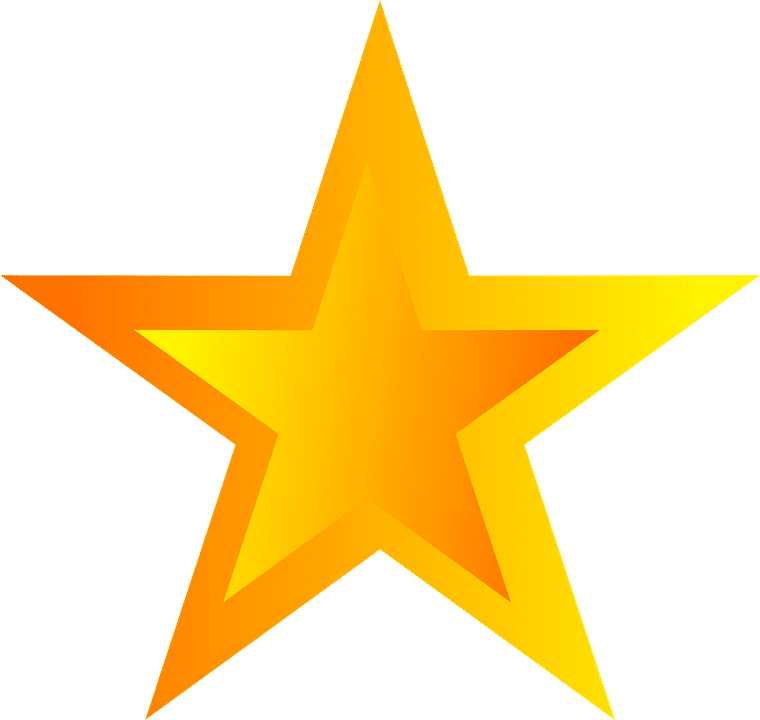
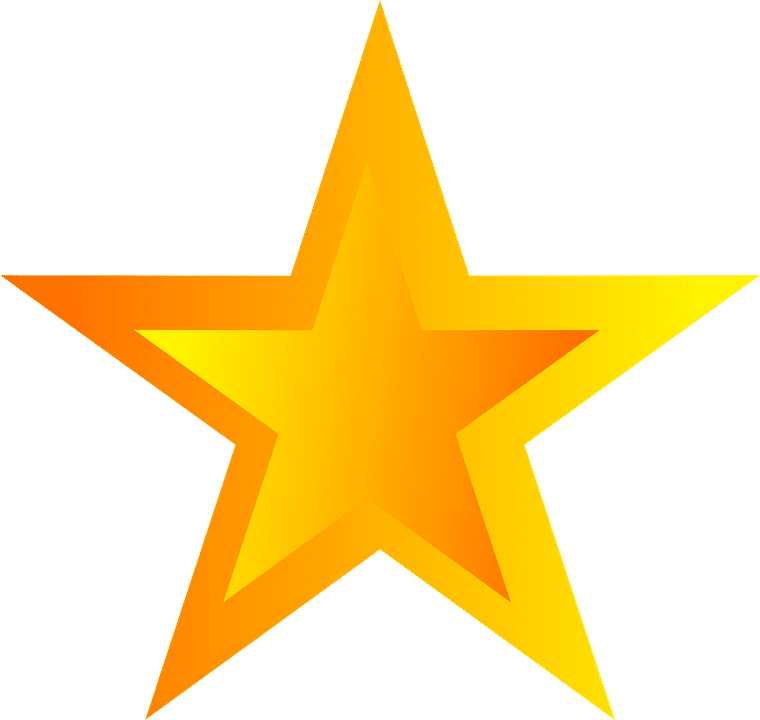
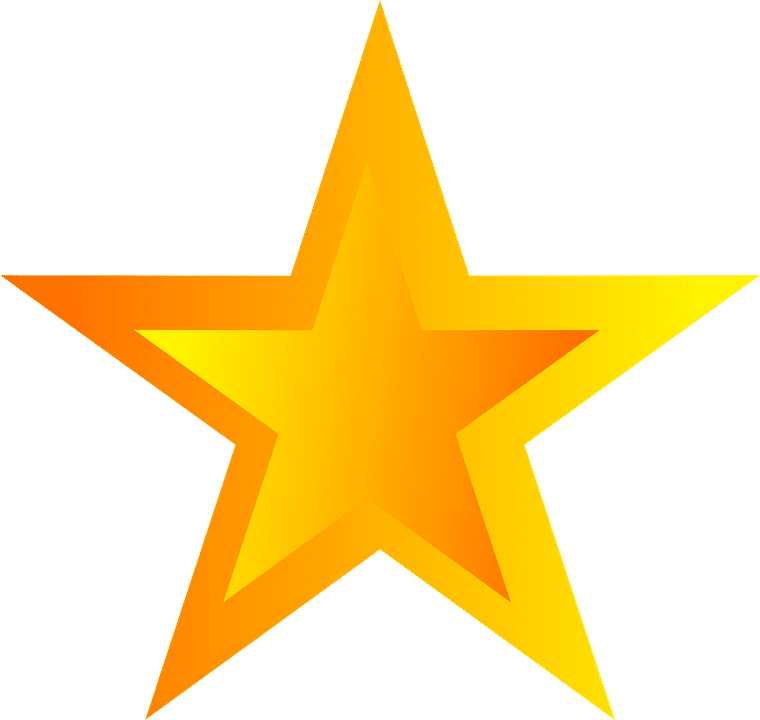
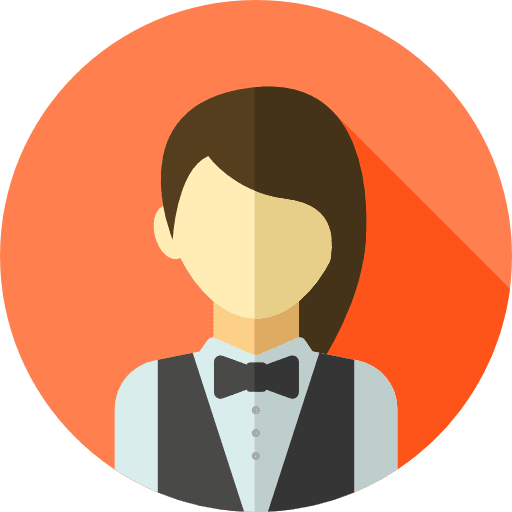
53 465
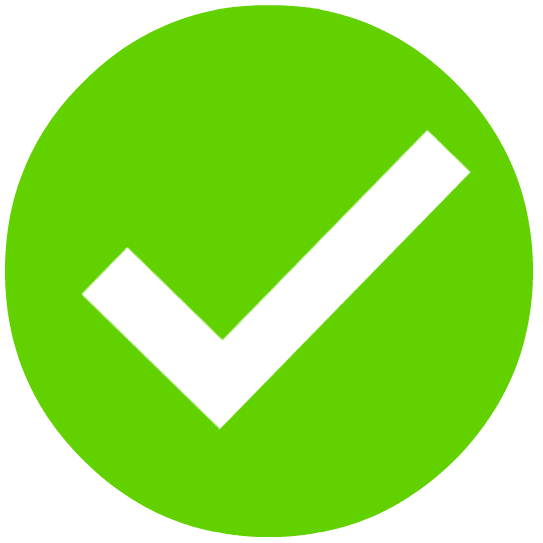
98%
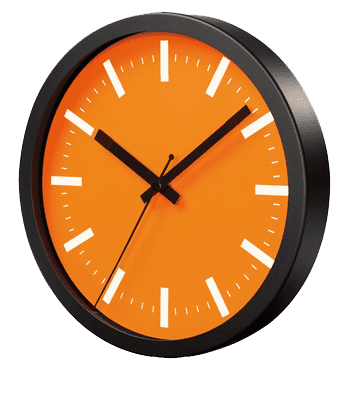
32