Blog

Ciężar objętościowy
W artykule znajdziesz:

Dzięki tym zaletom, jak również możliwości wykorzystania surowców miejscowych (wapna, piasku, żużla i popiołu), wykonywanie gazobetonu, gazoilikatu i gazożużlobetonu metodą autoklawizacji jest obecnie głównym kierunkiem rozwoju produkcji betonów komórkowych. Przy określaniu składu betonu komórkowego należy zapewnić uzyskanie wyznaczanego ciężaru objętościowego i jego największej wytrzymałości przy minimalnym zużyciu środka porotwórczego i spoiwa. Przy tym struktura betonu komórkowego powinna być utworzona przez równomiernie rozmieszczone drobne pory o prawidłowym kształcie kulistym (program uprawnienia budowlane na komputer).
Ciężar objętościowy betonu komórkowego i jego porowatość zależą głównie od zużycia środka pianotwórczego i stopnia wykorzystania jego zdolności porotwórczej. Na ich wielkość wywierają pewien wpływ temperatura mieszanki i przyjęta ilość wody do zarobienia mieszanki, tj. stosunek W/T (stosunek objętości wody do ciężaru spoiwa i dodatku krzemionkowego). Zwiększenie W/T powoduje wzrost ciekłości mieszanki, a zatem polepsza warunki powstawania porowatej struktury, jeśli zapewni się wystarczający opór penetracji mieszanki przed zakończeniem procesu wytwarzania się gazu (program uprawnienia budowlane na ANDROID).
Wytrzymałość betonu komórkowego zależy od jego porowatości, struktury porów i wytrzymałości błonek między porami. Ze zwiększeniem stosunku W/T do wartości optymalnej, zapewniającej najlepsze warunki formowania struktury mieszanki, wytrzymałość betonu komórkowego zwiększa się (uprawnienia budowlane).
Wytrzymałość błonek
Wytrzymałość błonek zależy z kolei od optymalnego stosunku spoiwa podstawowego (cementu, wapna lub cementu i wapna) i składnika krzemionkowego, od stopnia rozrzedzenia tego kompleksowego spoiwa wodą W/T, jak również od warunków obróbki cieplno-wilgotnościowej. Z betonu komórkowego o optymalnym składzie przygotowuje się próbki kontrolne, które bada się po obróbce cieplno-wilgotnościowej. Na podstawie wyników uzyskanych po ich zbadaniu uściśla się skład betonu, który powinien zapewnić uzyskanie materiału o założonym (nie większym) ciężarze objętościowym i o wymaganej marce (wytrzymałości) (program egzamin ustny).
Betonem silikatowym nazywa się sztuczny bezcementowy materiał kamienny, otrzymany w wyniku twardnienia w autoklawie mieszanki, składającej się z wapna lub innych materiałów wiążących na jego bazie, drobno rozproszonych dodatków krzemionkowych, piasku i wody. Główną substancją cementującą są hydrokrzemiany wapniowe o różnej zasadowości, powstające przy chemicznym współdziałaniu wodorotlenku wapniowego z krzemionką zawartą w rozproszonym dodatku lub piasku kwarcowym współdziałanie to znacznie intensyfikuje się w warunkach autoklawizacji, kiedy zwiększone ciśnienie pary nasyconej zapewnia zachowanie się w materiale wody w fazie ciekłej przy temperaturach przewyższających 100°C (opinie o programie).
Betony silikatowe wykonuje się najczęściej drobnioziarniste, tj. ich kruszywami są piaski kwarcowe i kwarcowo-skaleniowe. Pod względem struktury betony silikatowe mogą być zwarte ciężkie tylko na piasku kwarcowym) i zwarte lekkie (z kruszywem porowatym grubym lub drobnym). Odmianę betonów silikatowych stanowią betony poryzowane (gazosilikat i pianosilikat), które zalicza się do grupy betonów komórkowych. Drobnoziarniste zwarte betony silikatowe odznaczają się w porównaniu ze zwykłymi betonami cementowymi budową bardziej jednorodną, a także większą jednolitością struktury, dzięki charakterowi chemicznemu więzi między substancją cementującą i ziarnami kruszywa (segregator aktów prawnych).
Ciężkie betony silikatowe mają ciężar objętościowy 1800-2200 kG/cm2. Ich wytrzymałość na ściskanie waha się zwykle w granicach od 100 do 600 kG/cm2 i zależy od składu mieszanki, ustalonych warunków technologicznych autoklawizacji i innych czynników. Na przykład betony silikatowe twardniejące w autoklawach uzyskują wytrzymałość 100-300 kG/cm2 przy użyciu do ich wykonania wapna w ilości 8-11% ciężaru stałych składników i przy zagęszczaniu wibrowaniem. Przy dodaniu 15- 30% drobno mielonego piasku kwarcowego, dobrym zagęszczeniu mieszanki betonowej i optymalnych warunkach autoklawizacji wytrzymałość na ściskanie betonów silikatowych może być 2-3 razy większa i osiągnąć 400-600 kG/cm2 (promocja 3 w 1).
Najnowsze wpisy
Mostki akustyczne to newralgiczne miejsca w każdej konstrukcji budynku fragmenty ścian, stropów czy podłóg, którymi dźwięk może „przeskakiwać” z jednego…
Bogactwo asortymentu silikatowego wykracza daleko poza standardowe kształtki o wymiarach dostosowanych do najpowszechniej stosowanych grubości ścian. W ofercie producentów znaleźć…
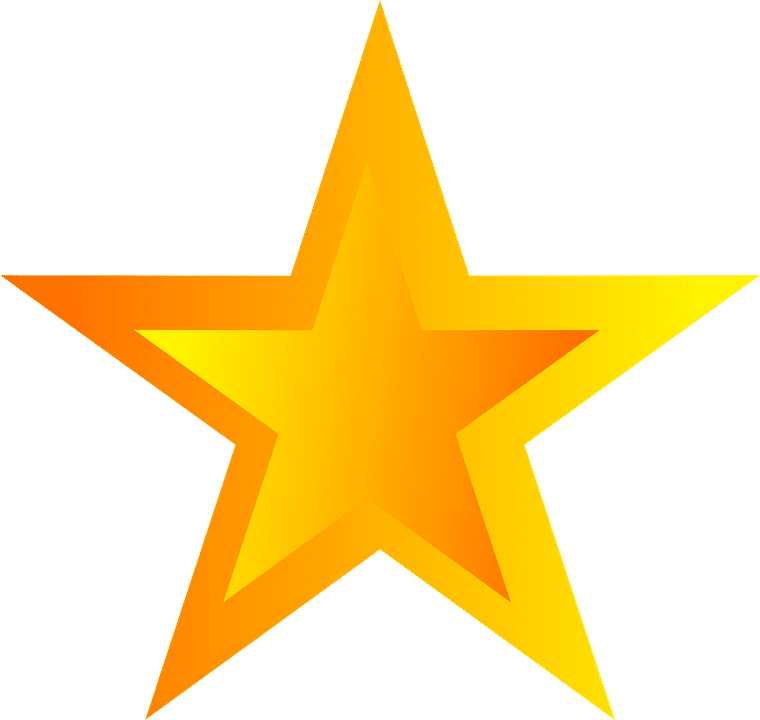
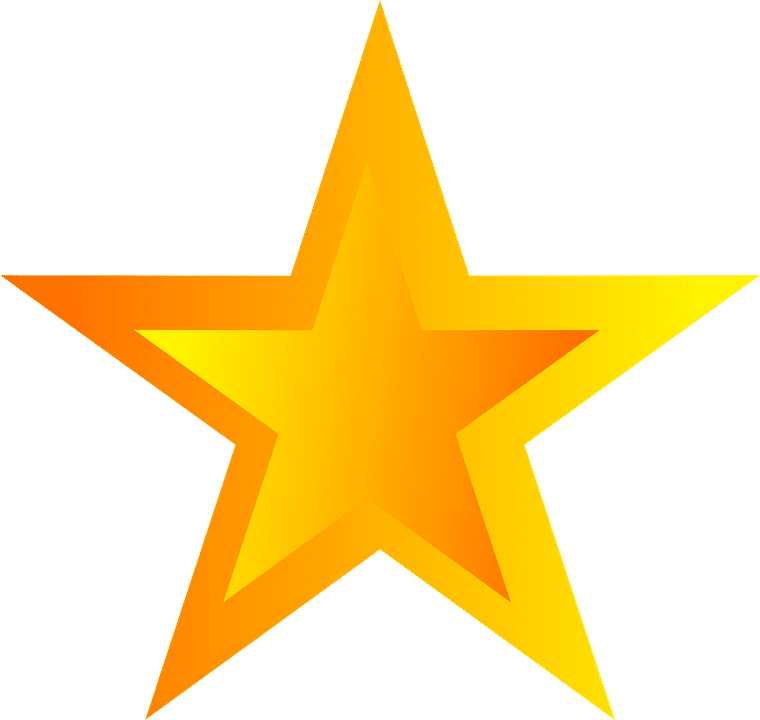
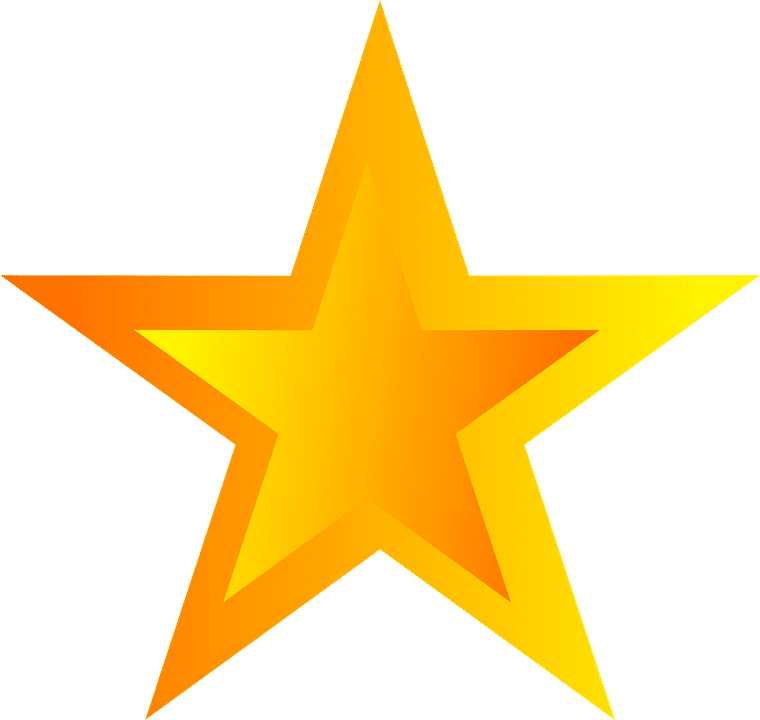
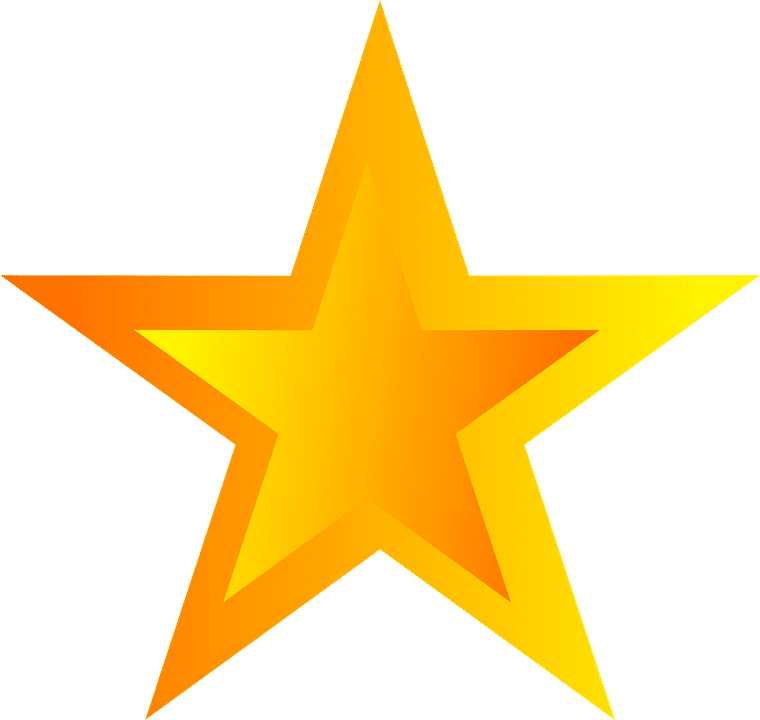
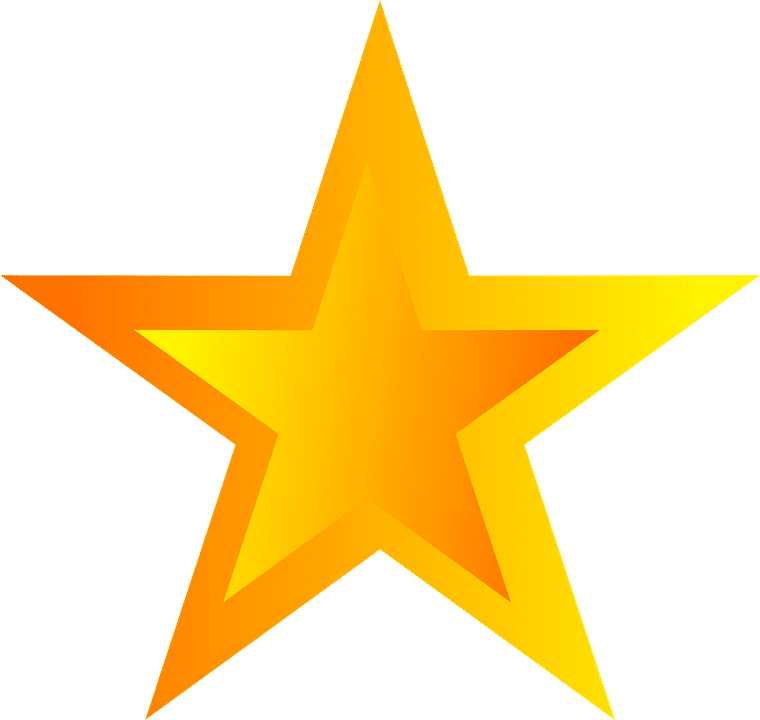
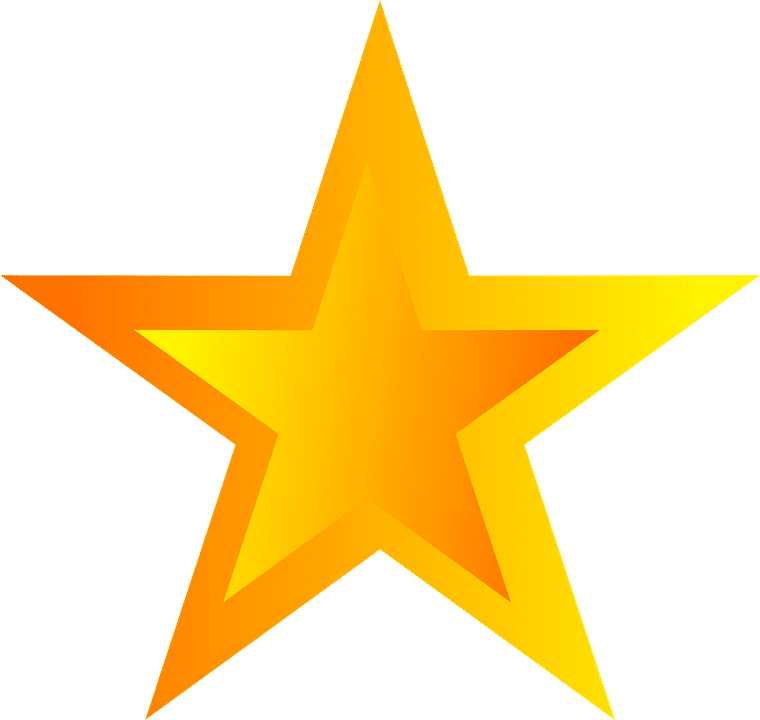
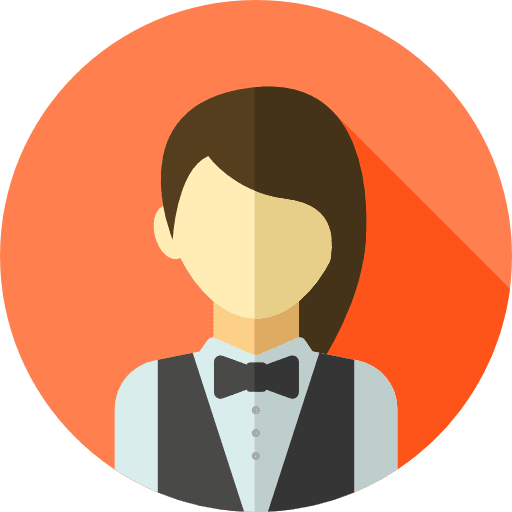
53 465
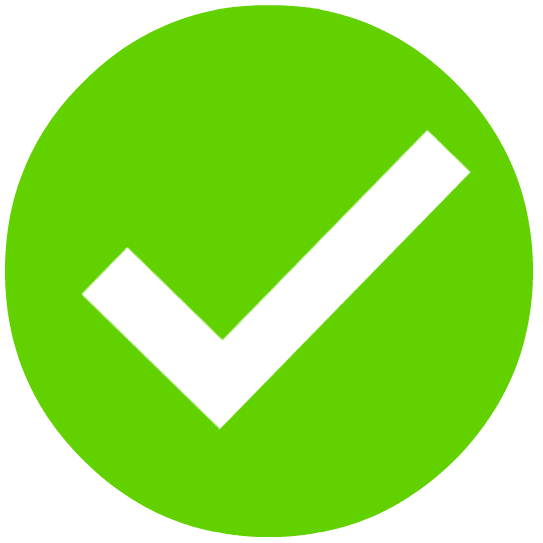
98%
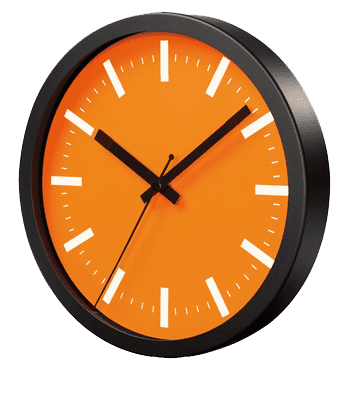
32