Blog
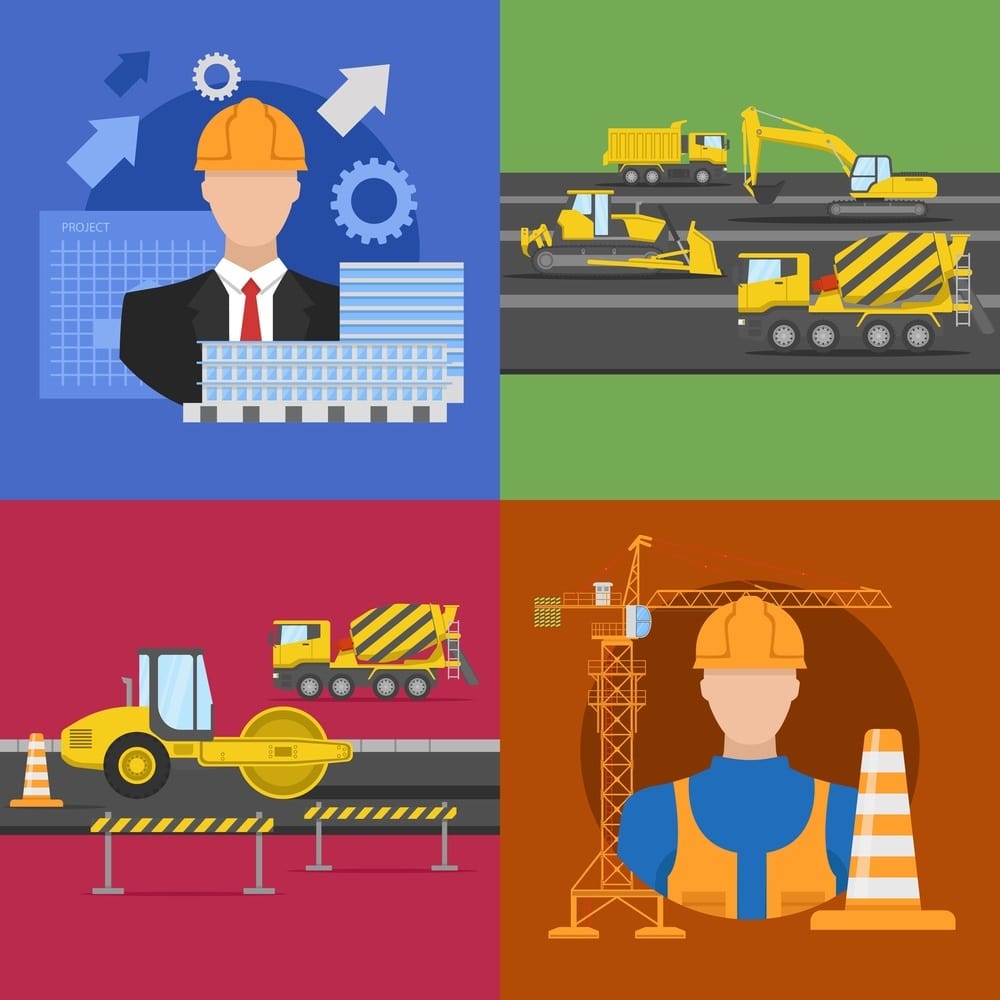
Części denne poziome
W artykule znajdziesz:
Części denne poziome

Części denne poziome każdej przepony w formach przeznaczonych do produkcji płyt stropowych przyspawane są do płyt przegrody, natomiast dna przegród w formach do produkcji ścian działowych są częściami oddzielnymi, opierającymi się na dolnych półkach ceowników konstrukcji rusztowania (program uprawnienia budowlane na komputer).
Pod elementami żelbetowymi zmontowanej formy bateryjnej w górnej części podłogi wykonane są komory grzejne, przez które przepuszcza się parę dla przyspieszenia ogrzewania pogrubionej części płyty. Główny przewód doprowadzający parę do obróbki termicznej umieszczony jest w górnej części formy. Do każdej przegrody parę doprowadza przewód gumowy o tak dobranej długości, aby można było rozsuwać przegrody bez odłączania przewodów (program uprawnienia budowlane na ANDROID).
Do zsuwania i rozsuwania przegród służą cztery prasy hydrauliczne o przedłużonych tłoczyskach przepuszczonych przez otwory we wspornikowych częściach konstrukcji wałków podporowych. Tłoczyska te mają na całej długości otwory do osadzania klinów. Kliny osadza się z jednej lub drugiej strony wsporników. W czasie pracy pras hydraulicznych kliny te naciskają na wsporniki i poruszają przegrody. Praca pras hydraulicznych oraz wszystkie czynności pracy baterii sterowane są ze stołu rozdzielczego.
produkcyjny przy stanie rozsuniętych przegród rozpoczyna się od starannego oczyszczenia i nasmarowania powierzchni zewnętrznych przegród gorącym roztworem nafty i tzw. „Petralotu", środka chemicznego, który powoduje szybkie tężenie smaru, tak że nie spływa on po ścianie przegrody (uprawnienia budowlane). W tak przygotowaną formę każdej przegrody opuszcza się za pomocą suwnicy szkielet zbrojenia i po umocowaniu go i sprawdzeniu właściwego jego położenia dosuwa się następną przegrodę. W ten sposób przeprowadza się kolejno montaż wszystkich komór i na zakończenie dociska się je prasami hydraulicznymi.
Wibrowanie betonu
W baterii typu NJAT zastosowano wibrowanie betonu w poszczególnych komorach przez wprawienie w drgania zbrojenia (program egzamin ustny). W tym celu do zbrojenia przytwierdza się wkład wibrujący, składający się z belki, dwóch kątowników 50 X 60 i wibratora. Wkład wibrujący przystosowany jest do wibrowania dwóch szkieletów w sąsiadujących komorach. Do kątowników wkładu dospawane są widełki, które po nasunięciu wkładu przenoszą drgania na wszystkie szkielety zbrojeniowe.
Po zmontowaniu baterii i nasunięciu wkładów wibracyjnych następuje napełnianie komór mieszanką betonową za pomocą sprężonego powietrza. Ze względu na pneumatyczny sposób napełniania zastosowano tu mieszankę drobnoziarnistą marki 200 o konsystencji półciekłej, o opadzie stożka opadowego H-ż-10 cm. Wskutek tego - dla uzyskania założonej wytrzymałości betonu - wystąpiła konieczność znacznego zwiększenia ilości spoiwa do ilości 600-650 kG na 1 m:i mimo zastosowania marek cementu portlandzkiego 400 i 500. Z drugiej strony nie można tu było użyć mieszanki o konsystencji plastycznej ze względu na niską efektywność zastosowanego sposobu wibrowania (opinie o programie).
Wszystkie komory wypełnia się mieszanką betonową jednocześnie przy uruchomionych wibratorach. Po zakończeniu formowania i zdjęciu wkładów wibrujących nakrywa się komory szczelnym brezentem i przeprowadza się obróbkę termiczną parą o maksymalnej temperaturze dochodzącej do 98°C w ciągu ośmiu godzin. Dopływ pary uruchamia się jeszcze w czasie betonowania, tak że z chwilą zakończenia formowania mieszanka betonowa jest już nagrzana. Dzięki temu w ciągu 30-60 minut beton osiąga założoną maksymalną temperaturę, która utrzymuje się przez 4-5 godzin. Po tym okresie wyłącza się dopływ pary i przez okres 2-3 godzin pozostawia beton w formach do ostudzenia. Po obróbce cieplnej beton elementów ociąga wytrzymałość równą 80-85% wytrzymałości normowej. Końcowymi czynnościami cyklu produkcyjnego jest kolejne rozsuwanie przegród, wyjmowanie gotowych płyt i ich transport na miejsce składowania (segregator aktów prawnych). W omówionym rozwiązaniu formy zmechanizowanej cykl produkcyjny jest krótszy o połowę od cyklu produkcyjnego przy zastosowaniu form niezmechanizowanych (około 12 godzin zamiast 24 godzin).
Produkcja elementów w formach bateryjnych o pracy ciągłej.
W najnowszych rozwiązaniach technologicznych elementy wielkopłytowe ścian wewnętrznych produkowane są w formach bateryjnych o pracy ciągłej (promocja 3 w 1). W metodzie tej, stosowanej przez duńską firmę S. Schmied, pomocnicze operacje produkcyjne jak: rozformowywanie, czyszczenie form, smarowanie form itp. odbywają się niezależnie od procesu formowania, co pozwala na zmniejszenie do minimum strat na te pomocnicze operacje, a tym samym umożliwia - przez skrócenie cyklu produkcyjnego - znaczne zwiększenie wydajności.
Najnowsze wpisy
W ostatnich latach rozwój sztucznej inteligencji (SI) gwałtownie przyspieszył, wkraczając niemal w każdą dziedzinę naszej codzienności. Nie inaczej jest w…
Rosnąca potrzeba przyspieszenia procesów budowlanych, ograniczenia kosztów i minimalizacji negatywnego wpływu branży na środowisko sprawia, że innowacyjne technologie przyciągają coraz…
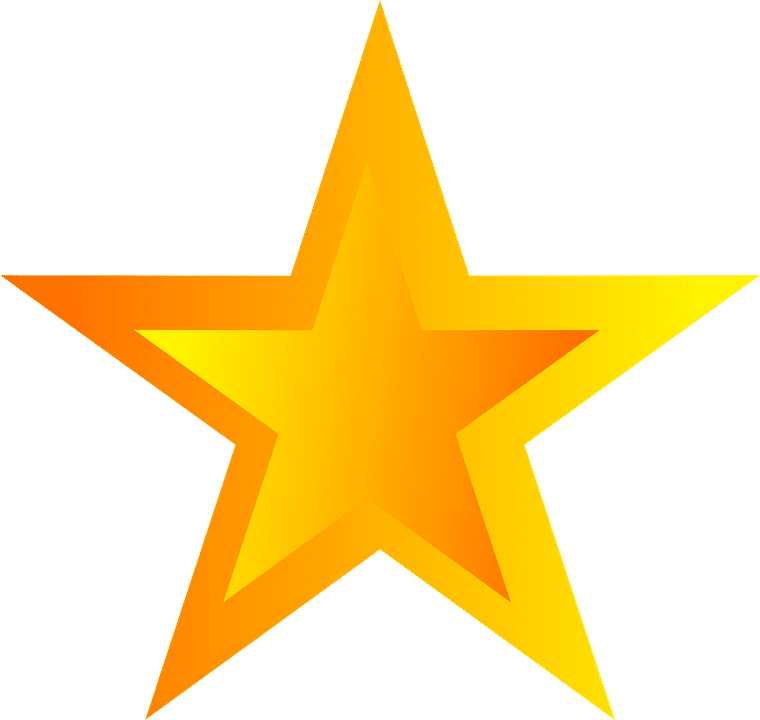
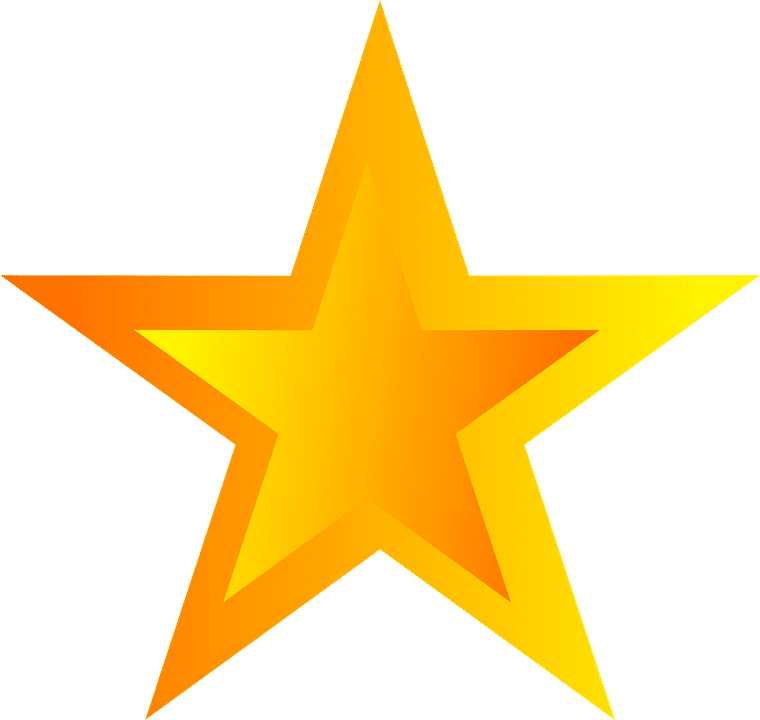
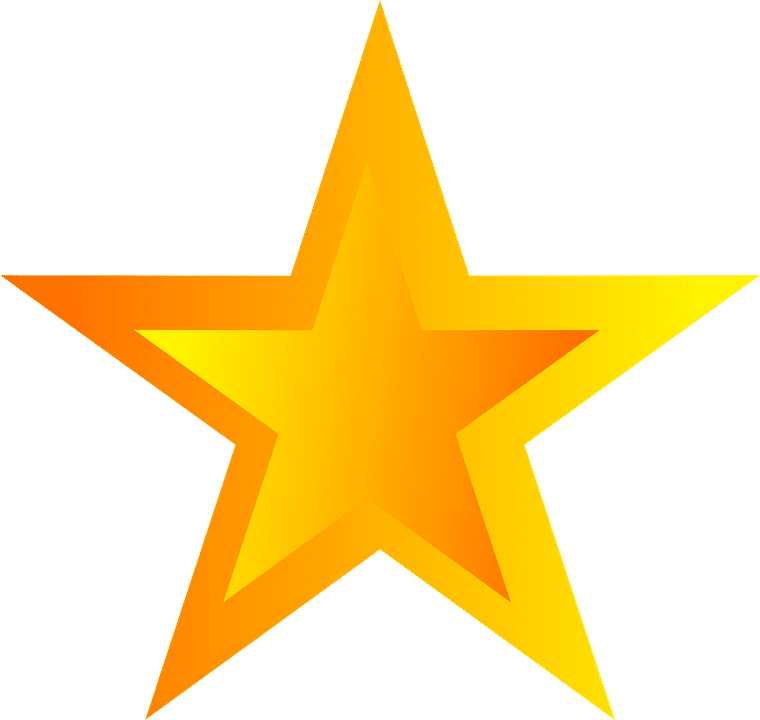
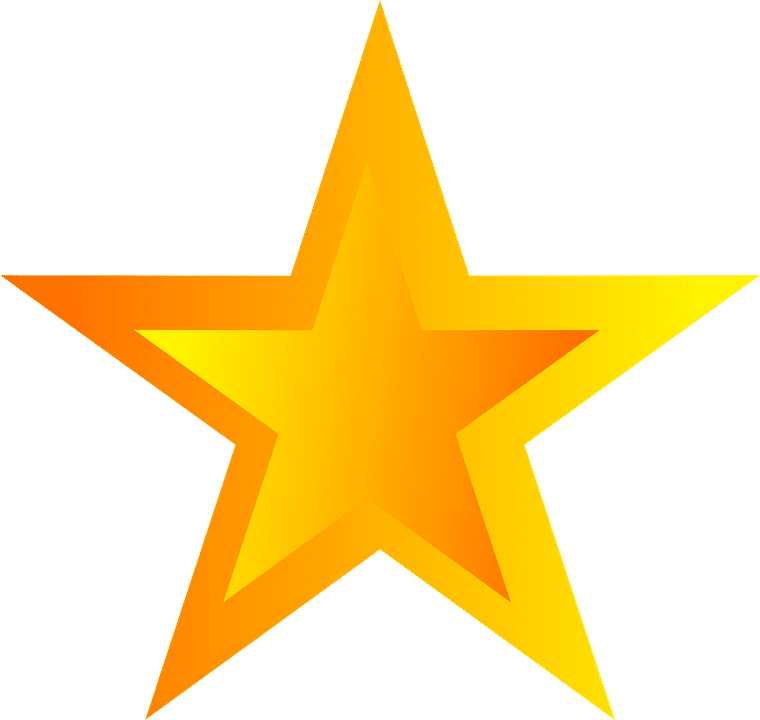
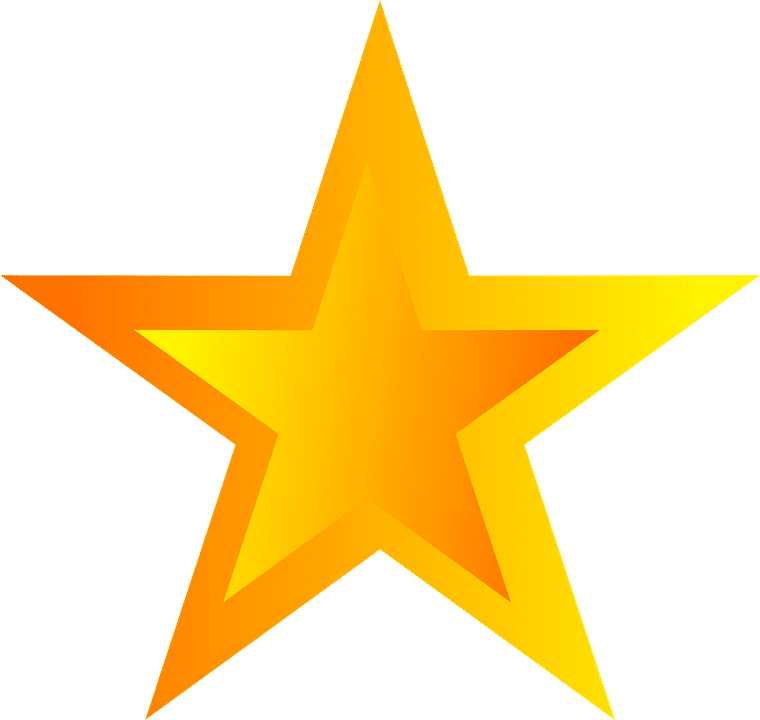
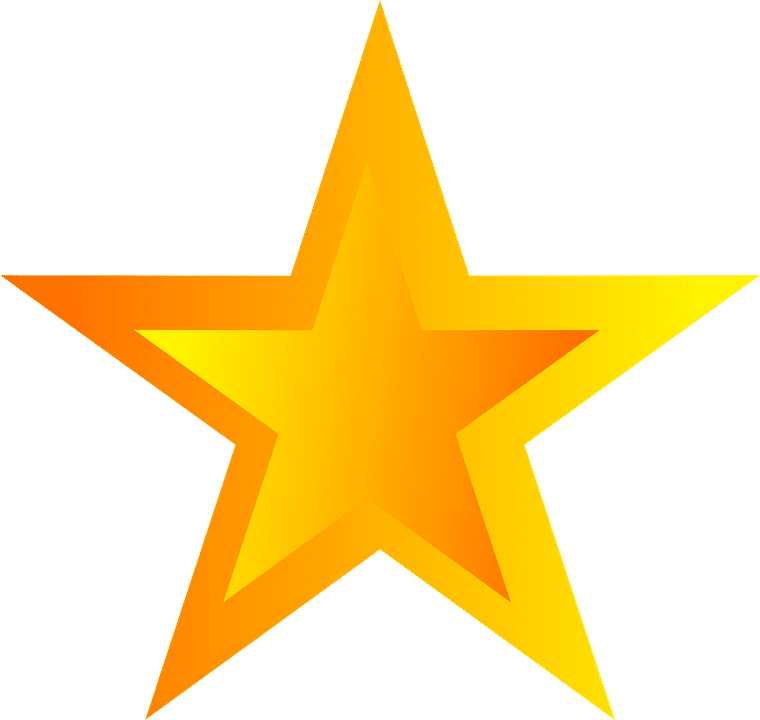
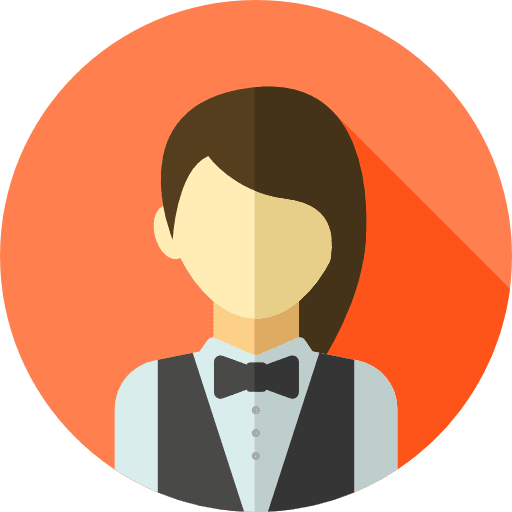
53 465
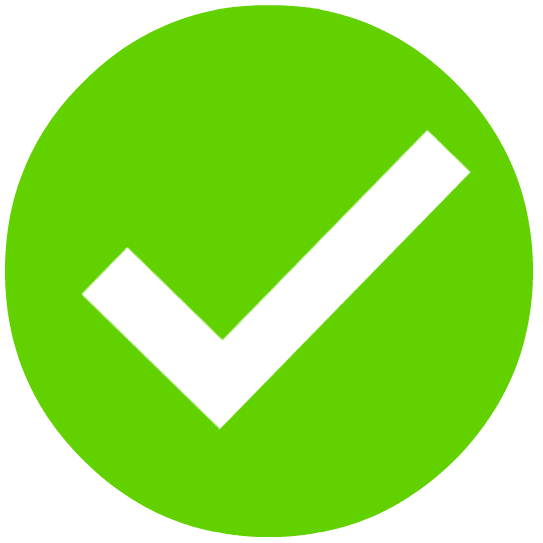
98%
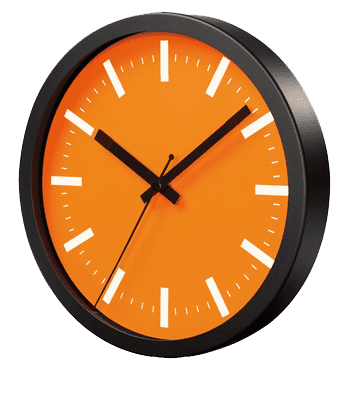
32