Blog
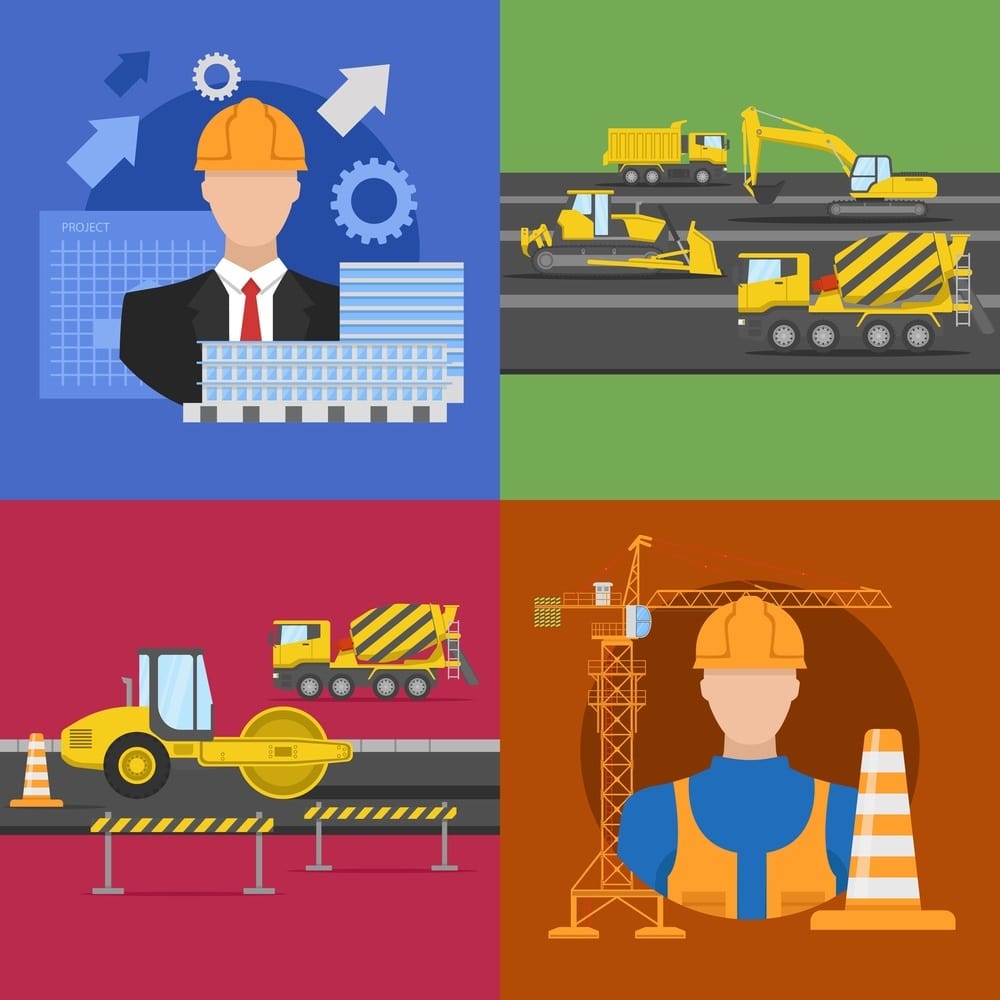
Dobór uziarnienia
W artykule znajdziesz:
Dobór uziarnienia

Dobór uziarnienia zapewnia optymalne zagęszczenie mieszanki, wyrażające się w minimalnej zawartości pustych przestrzeni między ziarnami kruszywa po ubiciu. Zawartość pustych przestrzeni zależy od uziarnienia i sposobu doboru mieszanki i waha się od 15 do 24% objętościowo, zależnie od rodzaju i uziarnienia składników masy bitumiczno-betonowej (program uprawnienia budowlane na komputer).
Znaleziona wartość pustych przestrzeni jest wskaźnikiem potrzebnej ilości lepiszcza bitumicznego, asfaltowego lub smołowego, koniecznego do ich wypełnienia i otoczenia ziarn kruszywa wchodzącego w skład mieszanki.
Ze względu na uziarnienie rozróżnia się następujące składy mas do układania nawierzchni bitumiczno-betonowych (asfaltowych i smołowych).
Mączki bitumiczne (z wapieni bitumicznych) do wyrobu asfaltów prasowanych (program uprawnienia budowlane na ANDROID).
Masa asfaltu piaskowego o składzie: piasek, wypełniacz, i asfalt jako lepiszcze. Masa ta stosowana jest do budowy nawierzchni drogowych, mostowych, podłóg hal fabrycznych oraz do produkcji płytek i cegieł prefabrykowanych.
Masa asfaltu lanego składająca się z grysiku kamiennego lub żwirku i wypełniacza w dużej ilości (20-30%) oraz z asfaltu jako lepiszcza. Znajduje ona bardzo szerokie zastosowanie do budowy nawierzchni drogowych, przemysłowych i wyrobu technicznych płytek prefabrykowanych oraz do celów izolacyjnych. Ze względu na dużą zawartość mączki i asfaltu masa ta posiada na gorąco konsystencję płynną. Ułożona w postaci warstwy lub płyty nie wymaga po ostygnięciu wałowania.
Asfaltobetony i smołobetony są to masy składające się z grysu granulowanego, piasku i wypełniacza; jako lepiszcze służy asfalt lub smoła (uprawnienia budowlane).
Masy o uziarnieniu powyżej 15 mm noszą nazwę betonów bitumicznych gruboziarnistych, do 15 mm średnioziarnistych oraz do 5 mm drobnoziarnistych.
Masy bitumiczno-betonowe stosowane są głównie do budowy nawierzchni drogowych i podłóg w halach fabrycznych oraz do wyrobu prefabrykatów w postaci bloków i płyt.
Technologia produkcji
Technologia produkcji i układania mas bitumiczno-betonowych obejmuje następujące czynności:
- dobór mieszanki mineralnej, złożonej z poszczególnych frakcji grysów, piasku oraz mączki mineralnej,
- przygotowanie lepiszcza asfaltowego lub smołowego,
- otoczenie mieszanki mineralnej lepiszczem na gorąco lub na zimno w zależności od rodzaju i przeznaczenia masy (program egzamin ustny),
- przewiezienie masy bitumicznej na miejsce użycia, rozłożenie i zagęszczenie przez ubijanie lub zawałowanie.
Ze względu na sposób przygotowywania masy, tj. otoczenia ziarn bitumem, rozróżnia się masy asfaltobetonowe i smołobetonowe, otaczane na gorąco lub na zimno.
Przy systemie produkcji na gorąco mieszankę mineralną otacza się asfaltem lub smołą w specjalnych mieszarkach (opinie o programie).
Lepiszcze zostaje podgrzane uprzednio do temperatury zapewniającej mu zupełną płynność (temperatura: 16O-hl70cC dla asfaltu, a 80-M10 C dla smoły). Przy produkcji na zimno mieszankę mineralną otacza się asfaltami lub smołami upłynnionymi względnie emulsjami, umożliwiającymi mieszanie bez podgrzewania.
Masa produkowana w ten sposób jest układana i zagęszczana w stanie zimnym, podczas gdy masy produkowane przy wymieszaniu podgrzanej mieszanki mineralnej z gorącym asfaltem lub smołą, jako tzw. masy gorące, układane i zagęszczane są w stanie gorącym (segregator aktów prawnych).
Możliwe jest ponadto przygotowanie mas bitumicznych na gorąco i stosowanie ich w stanie zimnym po przestudzeniu. Szczególnie dotyczy to mas smołowych.
Płyty, bloki, wyroby specjalne asfaltowe lub smołowe przygotowuje się z odpowiednio dobranych mas bitumiczno-betonowych.
Najprostszą odmianą tego typu są płyty i płytki prasowane ze sproszkowanych wapieni bitumicznych. Obecnie stosuje się częściej masy bitumiczno-betonowe, zestawione na gorąco. Masami tego rodzaju wypełnia się formy stalowe o odpowiednim kształcie i przez prasowanie pod ciśnieniem 250-300 kG/cm2 formuje się płyty lub bloki, które po wyjęciu nadają się do bezpośredniego użycia (promocja 3 w 1).
Najnowsze wpisy
W ostatnich latach rozwój sztucznej inteligencji (SI) gwałtownie przyspieszył, wkraczając niemal w każdą dziedzinę naszej codzienności. Nie inaczej jest w…
Rosnąca potrzeba przyspieszenia procesów budowlanych, ograniczenia kosztów i minimalizacji negatywnego wpływu branży na środowisko sprawia, że innowacyjne technologie przyciągają coraz…
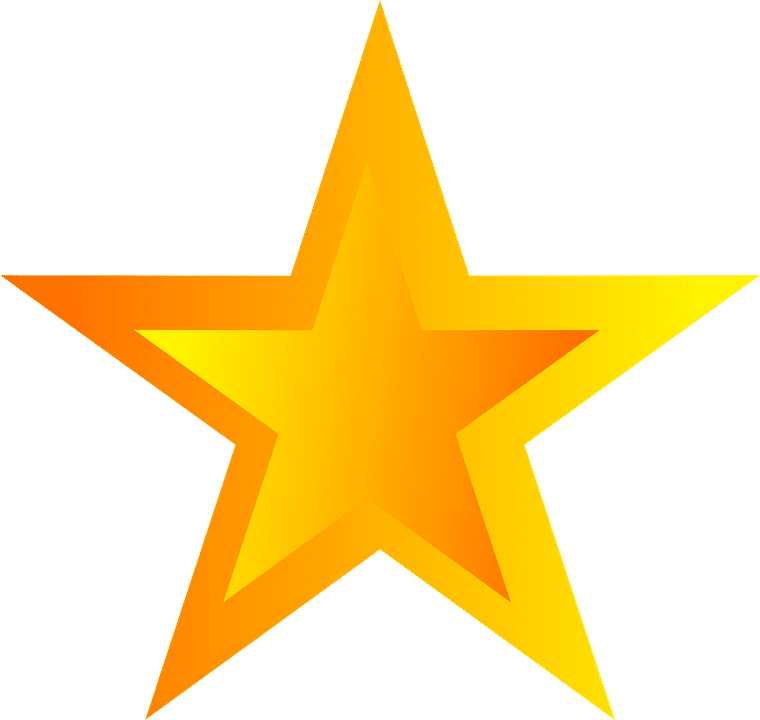
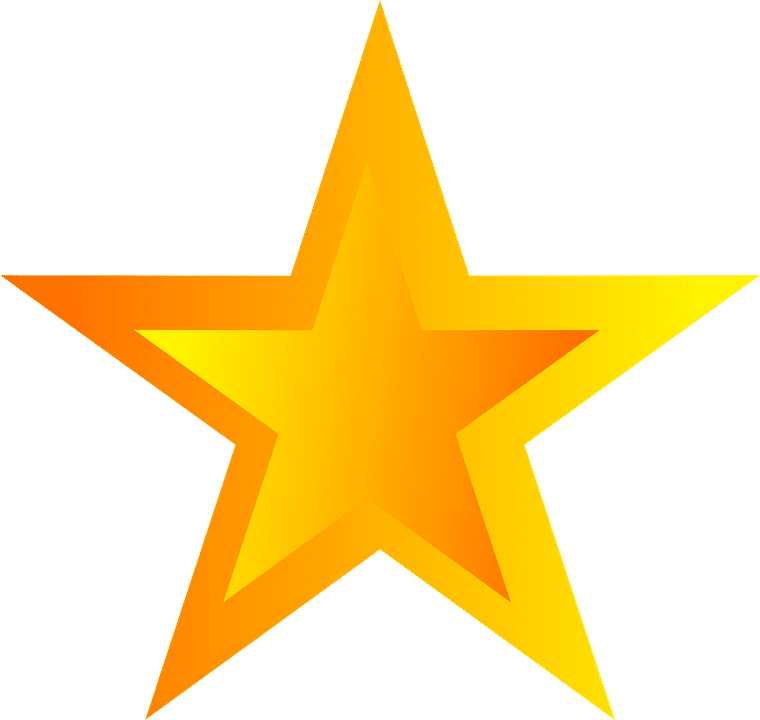
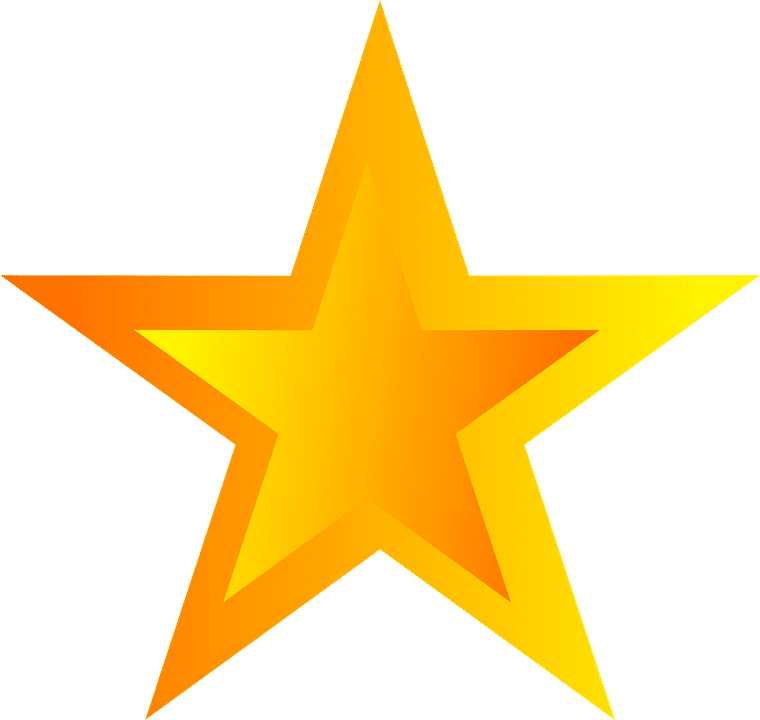
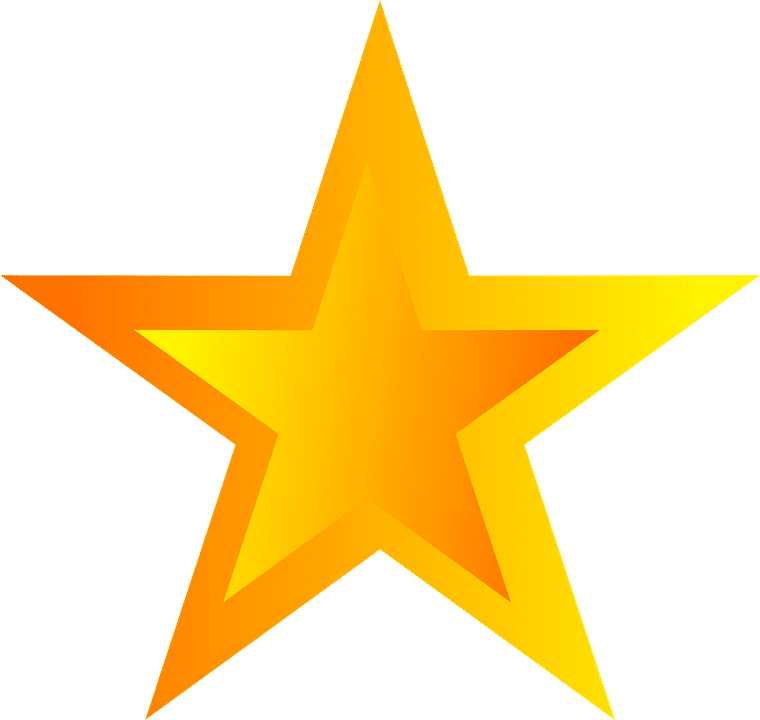
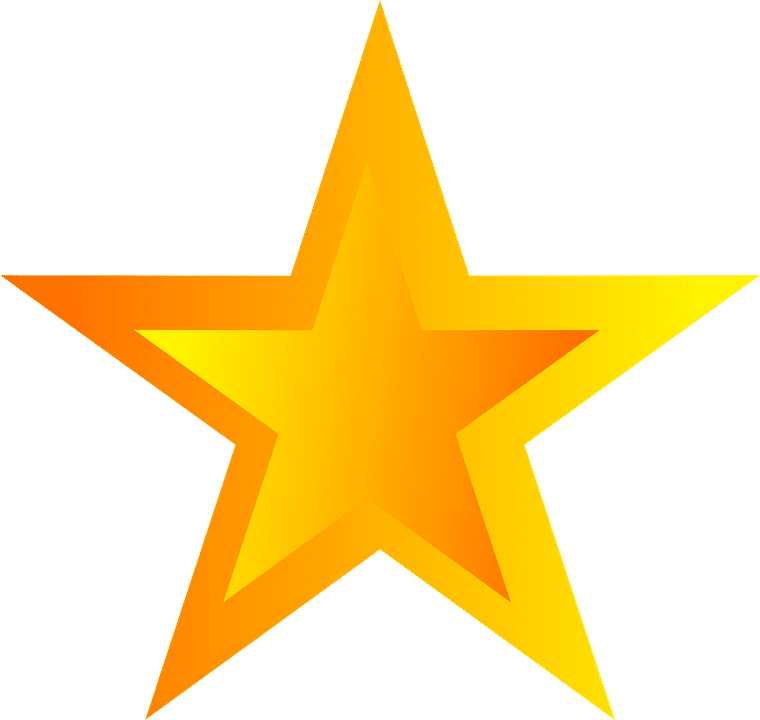
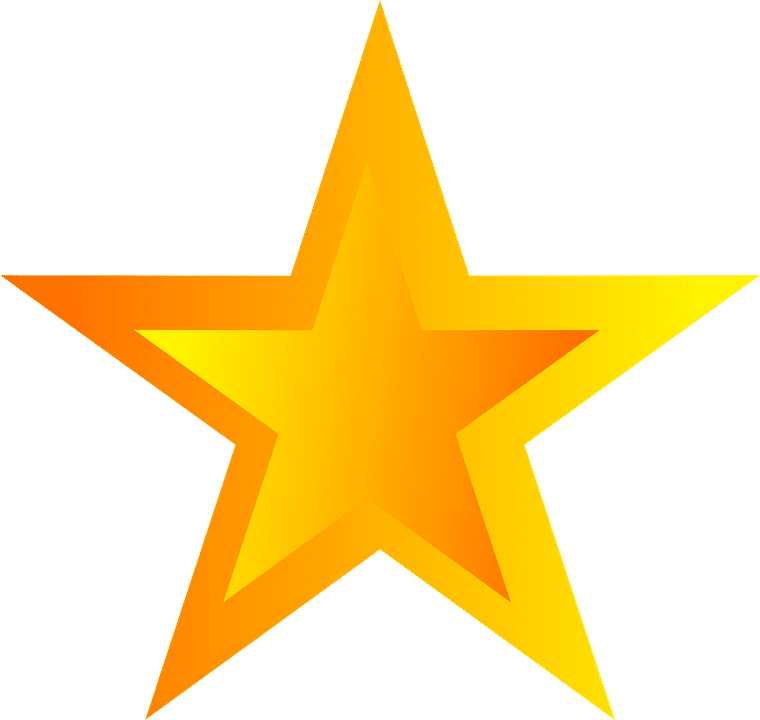
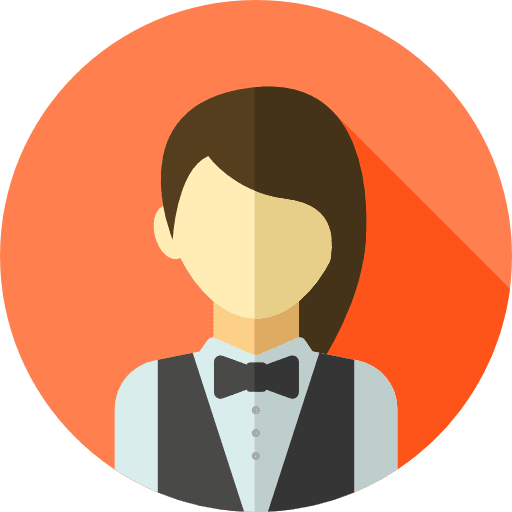
53 465
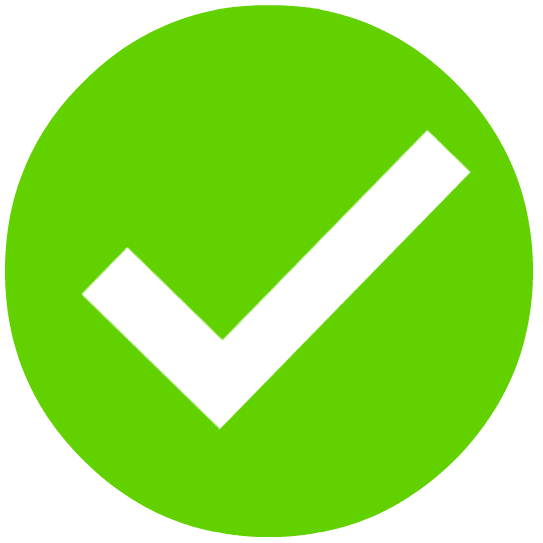
98%
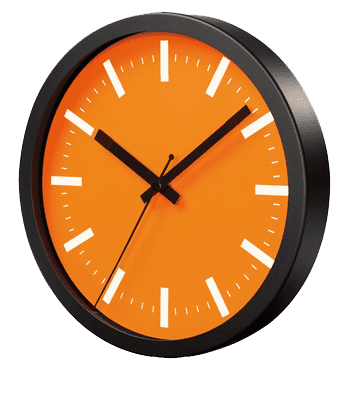
32