Blog
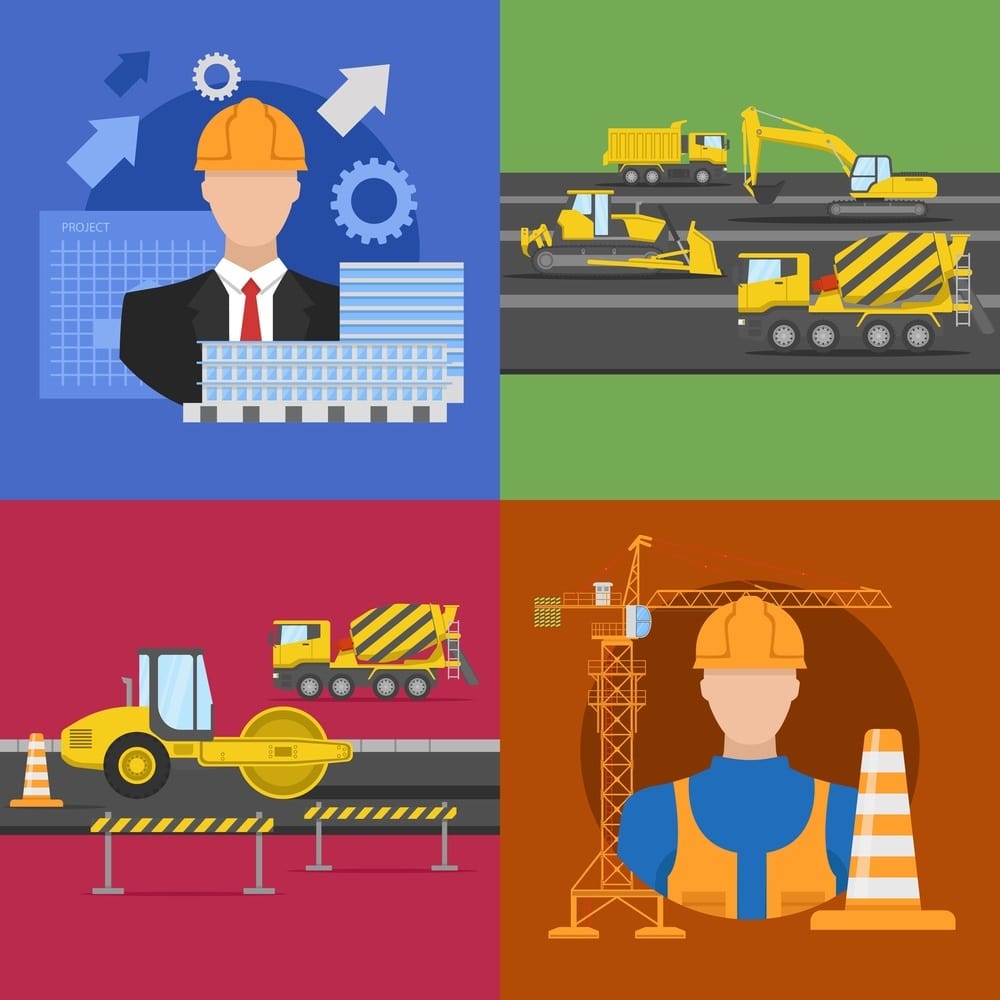
Płyta dociskowa uprawnienia budowlane
W artykule znajdziesz:
Płyta dociskowa uprawnienia budowlane

Produkcja płyt wielootworowych na stojakach wibracyjnych z płytą dociskową i obróbką termiczną w stosach. Technologia produkcji na stojakach wibracyjnych z płytą dociskową i obróbką termiczną w stosach zastosowana została jako typowa w wielu naszych wytwórniach (w Kurzętniku, Ełku, Łodzi, Sitkówce) przy produkcji płyt otworowych stropowych i otworowych bloków ściennych (program uprawnienia budowlane na komputer). Rozwiązanie to przyjęto głównie ze względu na możliwość zastosowania go w istniejących zakładach po ich niewielkiej stosunkowo modernizacji Technologia ta charakteryzuje się zastosowaniem urządzeń formujących w postaci podkładów i form stalowych z rozsuwanymi bokami oraz urządzeń zagęszczających w postaci zespołu 4 stojaków wibracyjnych - zamiast stołów wibracyjnych - na których spoczywają podkłady. Dla zmniejszenia ilości podkładów potrzebnych produkcji przyjęto dwie ich wielkości: podkład 650 X 160 cm dla element o szerokości 119 i 89 cm oraz podkład 650 X 190 cm dla elementów o szerokości 149 cm, z tym że elementy o długościach do 286 cm mogą być formowane po 2 sztuki na podkładzie (program uprawnienia budowlane na ANDROID).
Do podstawowego wyposażenia linii produkcyjny należą: kosz zasypowy z wyciągiem, samojezdny zasypnik betonu, przeciągarka rdzeni, zestaw stojaków wibracyjnych, suwnica do przenoszeni podkładów za pomocą zawiesia na poszczególne stanowiska oraz podkładów stalowych o podwójnych blachach, tworzących formę koszulkową do obróbki termicznej łącznie z zestawem form ramowych rozsuwanych, stanowiących pionowe części boczne formy (uprawnienia budowlane). W technologii tej rozróżnić można następujące podstawowe stanowiska produkcyjne: stanowisko A czyszczenia i smarowania podkładów, stanowisko B zakładania form ramowych na podkłady i układania w formie zbrojenia i stanowisko C formowania i zagęszczania betonu. Podkłady przesuwane są ręcznie ze stanowiska A na stanowisko B i C po przenośniku rolkowym, który stanowi przedłużenie podstawowego stanowiska formowania.
Przygotowane do formowania zazbrojone podkłady zostają przesunięte na urządzenia rolkowe przenośnikowe, które przenoszą je na stanowisko formowania, gdzie podkłady zostają opuszczone na stojaki wibracyjne. Na stanowisku formowania przeprowadza się następujące czynności: nasunięcie na podkład zespołu rdzeni za pomocą przeciągarki rdzeni, naniesienie mieszanki betonowej za pomocą samojezdnego zasypnika betonu przy uruchomionej pracy stojaków wibracyjnych, nałożenie płyty dociskowej ii na beton w końcowym stadium zagęszczania oraz po zakończeniu procesu zagęszczania - wyciągnięcie rdzeni i zdjęcie płyty dociskowej (program egzamin ustny).
Element przenoszony
Po uformowaniu element przenoszony jest wraz z podkładem na jedno ze stanowisk obróbki termicznej D za pomocą suwnicy.
Podkłady wraz z elementami w formach ramowych układane są do obróbki termicznej w stosach, jedne na drugich, po 6 sztuk w stosie. Stosy te ustawiane są na stalowych ramach, obejmujących punkty doprowadzenia pary w posadzce. Obróbka termiczna elementów parą doprowadzoną przewodami gumowymi do pokryw koszulkowych trwa 9 godzin. Po ukończeniu obróbki termicznej przenosi się suwnicą poszczególne podkłady z elementami na stanowisko studzenia E, a po ostudzeniu elementów na stanowisko rozformowywania F, gdzie zdejmuje się suwnicą najpierw formę ramową, a następnie płytę. Płytę przenosi się z kolei na wózek platformowy na stanowisko G, a zwolniony podkład ustawia się na stanowisku A do następnego cyklu produkcyjnego. Gotowe elementy wywozi się ze stanowiska G wózkiem po torze szynowym na plac składowy (opinie o programie).
Czas formowania elementu wynosi w tej technologii 14 i 20 minut, cykl produkcyjny - 24 godziny, wskaźnik wydajności produkcji na jednostkę powierzchni produkcyjnej przy pracy 2-zmianowej - 19 mVm2/rok, wskaźnik wydajności pracy - 715 m3/rob./rok, wielkość rocznej produkcji - 100 m płyt otworowych. Powyższa technologia została u nas zastosowana również do produkcji dachowych płyt żelbetowych żebrowych. Poza omówionym rozwiązaniem zostały opracowane u nas jeszcze inne rozwiązania charakteryzujące się wysokim zmechanizowaniem linii technologicznych.
Jedno z tych wysoko zmechanizowanych rozwiązań z częściową automatyzacją procesów produkcyjnych zostało zastosowane w Ostrowcu Wielkopolskim. Rozwiązanie to cechuje znaczniejsze niż w wyżej omówionym przykładzie rozdzielenie operacji przygotowawczych na osobne stanowiska urządzone na ciągu rolek transportowych (segregator aktów prawnych). Ciąg ten powiązany jest ze stanowiskiem formowania oraz stanowiskami studzenia i załadunku elementów specjalnymi wózkami transportowymi, poruszającymi się po napowietrznych torach, wyposażonymi każdy w 2 elektrowyciągi.
Przez zastosowanie tego rodzaju wózków transportowych praca suwnicy ograniczona została jedynie do obsługi stanowiska (stosów) obróbki termicznej i do zdejmowania formy ramowej z podkładu po zaformowaniu elementu. Po obróbce termicznej element wraz z podkładem przenoszony jest suwnicą z jednego ze stosów na stanowisko rozformowywania znajdujące się w zasięgu dwu elektrowciągów (promocja 3 w 1).
Najnowsze wpisy
W ostatnich latach rozwój sztucznej inteligencji (SI) gwałtownie przyspieszył, wkraczając niemal w każdą dziedzinę naszej codzienności. Nie inaczej jest w…
Rosnąca potrzeba przyspieszenia procesów budowlanych, ograniczenia kosztów i minimalizacji negatywnego wpływu branży na środowisko sprawia, że innowacyjne technologie przyciągają coraz…
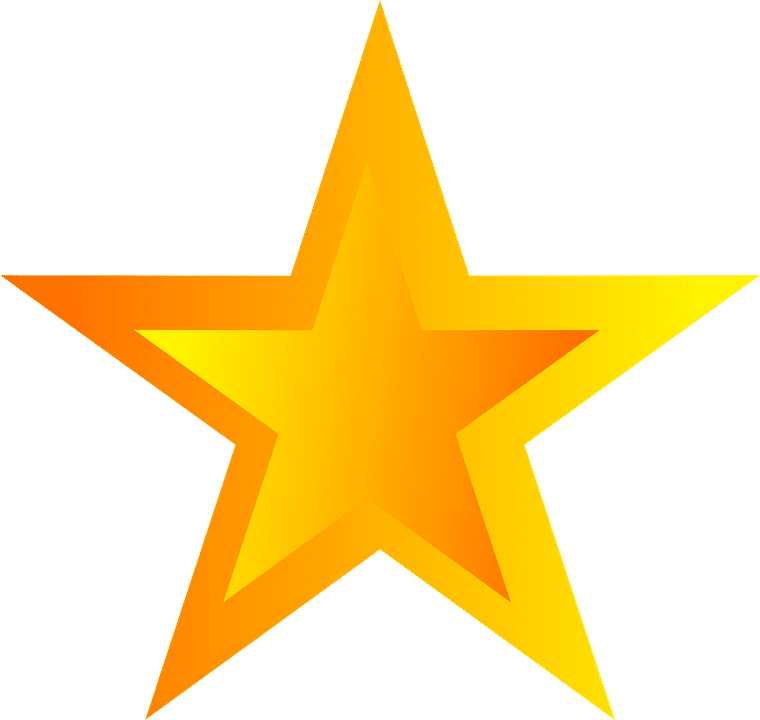
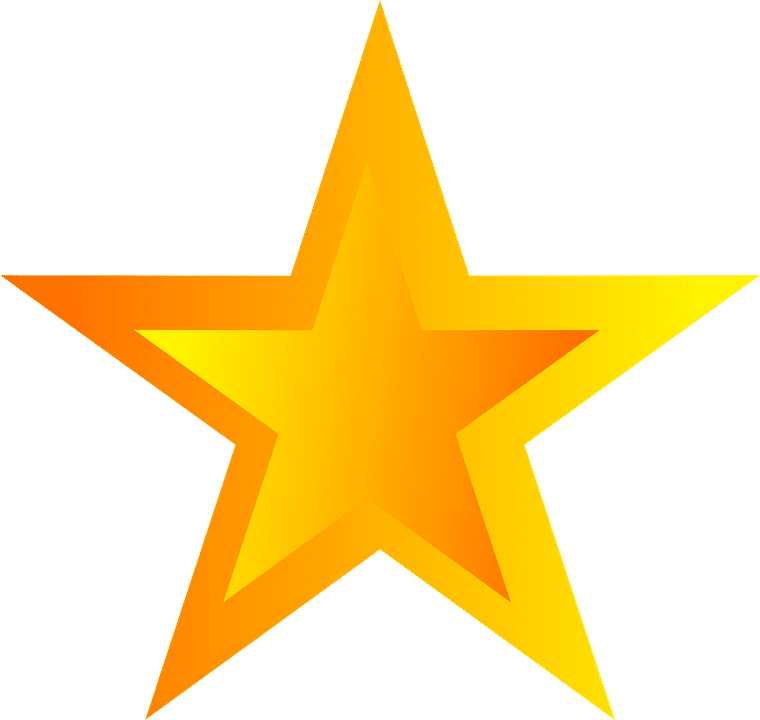
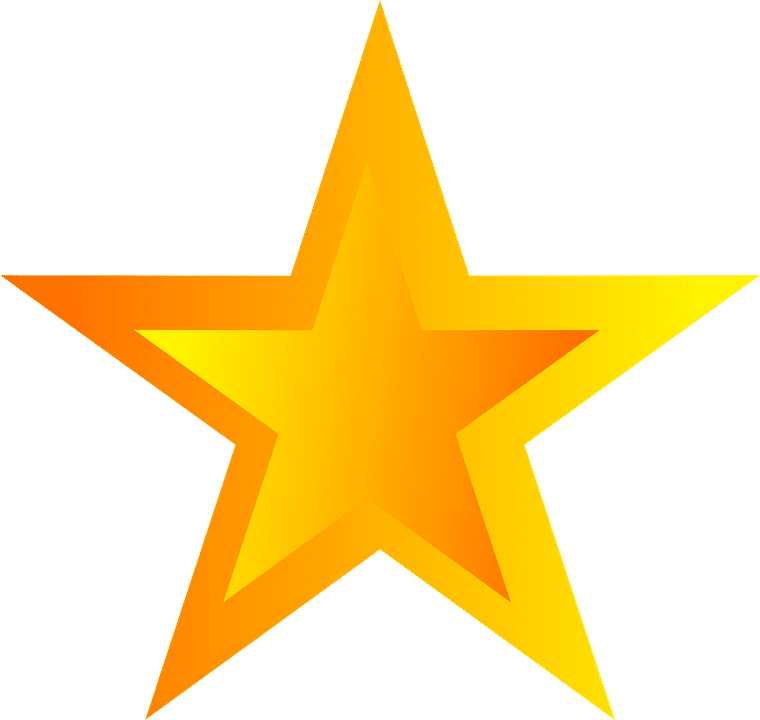
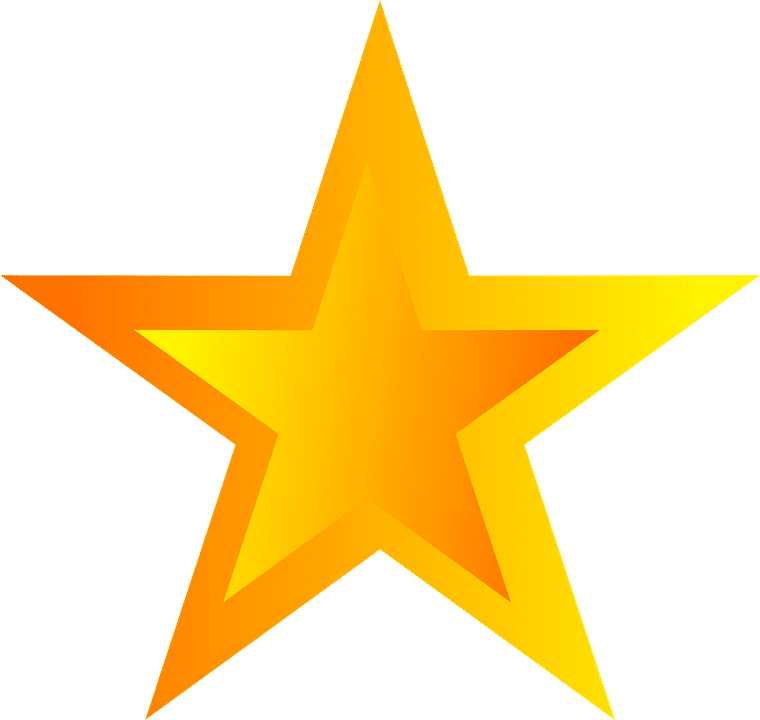
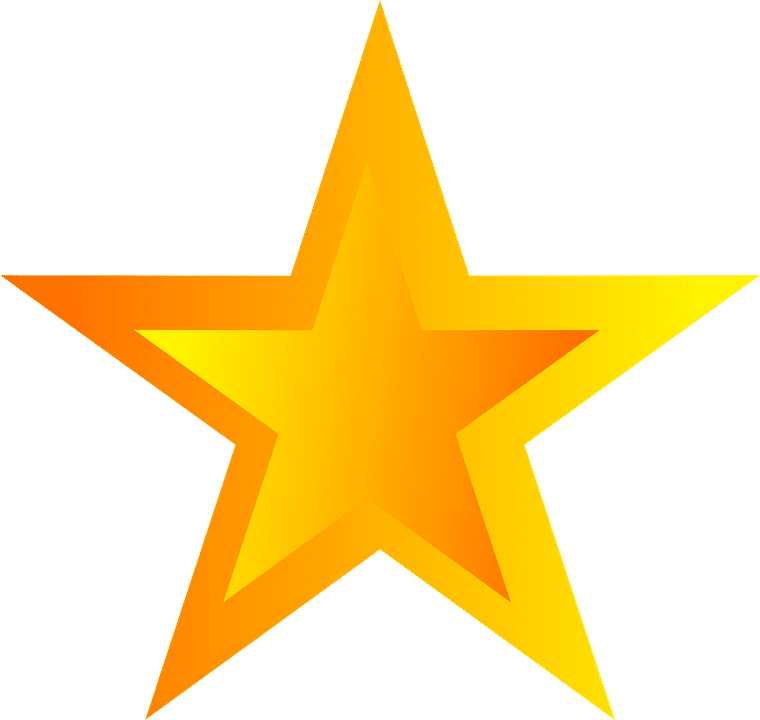
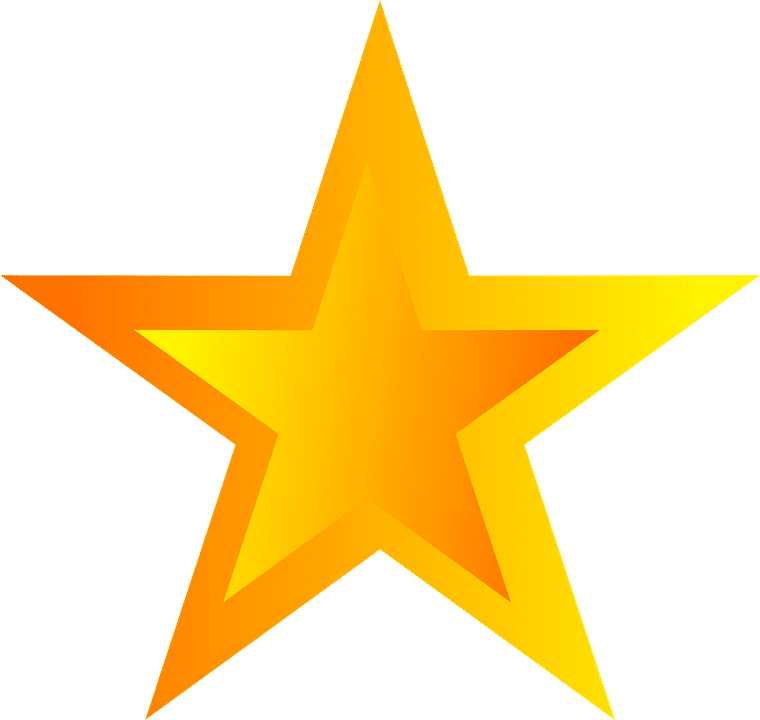
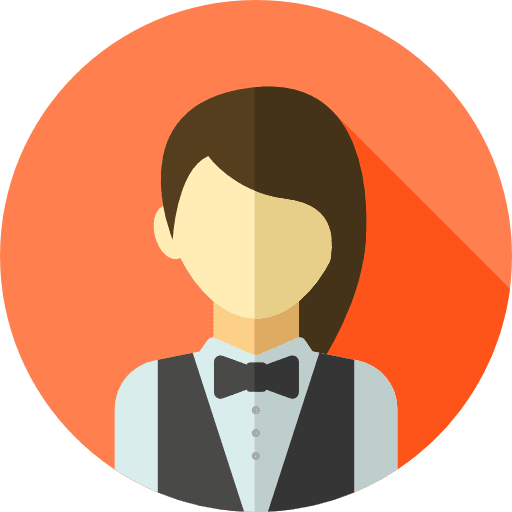
53 465
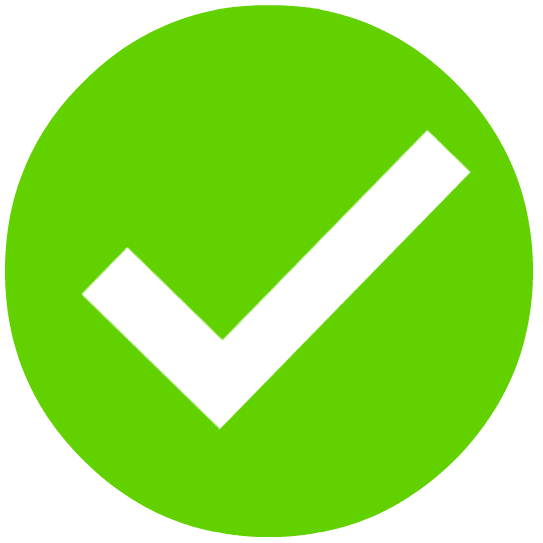
98%
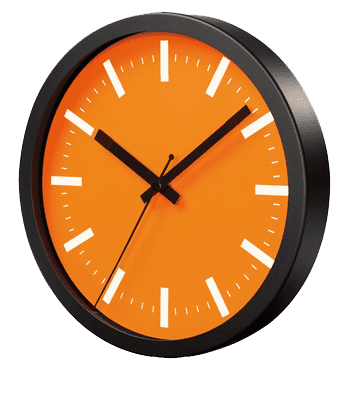
32