Blog
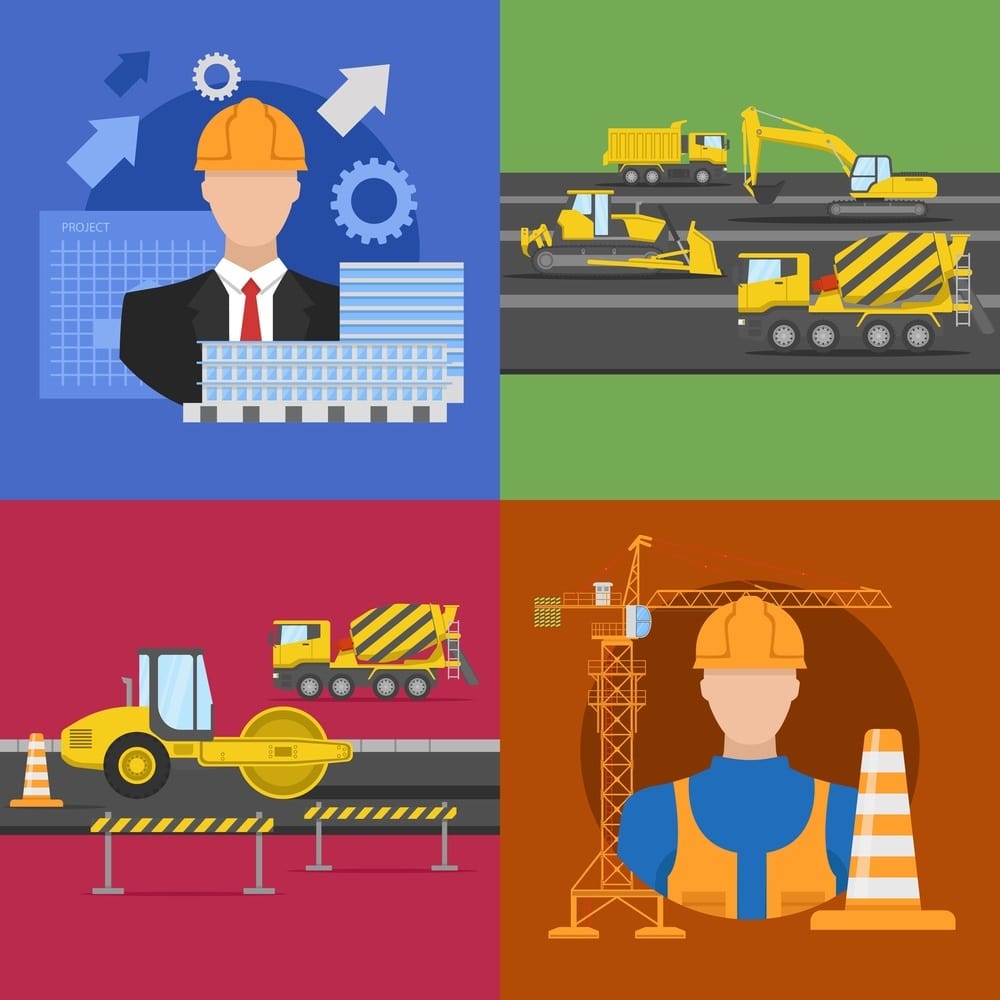
Produkcja uprawnienia budowlane
W artykule znajdziesz:
Produkcja uprawnienia budowlane

Produkcja polega na przemieleniu surowców, uzyskaniu jednorodnego, nierozwarstwiającego się i nieosiadającego szlamu oraz utwardzenie szlamu w formach stalowych za pomocą autoklawizacji (program uprawnienia budowlane na komputer). Jako stabilizator stosuje się roztwór sodowy szkła wodnego w ilości od 1 do 5% zależnie od ciężaru objętościowego materiału.
Cykl naparzania wyrobów w autoklawach składa się z podnoszenia ciśnienia pary do 8 at n w ciągu 3 godz., utrzymywania ciśnienia w ciągu 8 godz., obniżania ciśnienia w ciągu 5 godz. Z mikroporytu produkowanego w ZSRR wyrabiane są kształtki i płyty do izolacji termicznej o ciężarze objętościowym 500 kG/m3 oraz płyty na ścianki działowe o ciężarze objętościowym 600-700 kG/m3.
Zarówno turyt jak i mikroporyt nie są odporne na działanie mrozu w stanie nasycenia wodą (program uprawnienia budowlane na ANDROID). Poza tym w materiałach tych występują naprężenia wewnętrzne, co ogranicza wymiary elementów, a przy płytach ich grubość (do 8-10 cm).
Silikork. Beton lekki o strukturze mikroporowatej produkowany w CSRS nosi nazwę silikork. Jako surowiec krzemionkowy stosuje się popioły lotne, tzw. si-sztof, i mielony piasek kwarcowy. Spoiwem jest wapno. Poza tym stosuje się dodatki azbestu krótkowłóknistego, wyczeszek tekstylnych i cukru technicznego (melasa). Z silikorku wyrabia się płyty na ścianki działowe oraz płyty na ściany zewnętrzne i stropy. Te ostatnie są pokrywane powłoką hydrofobową (uprawnienia budowlane).
W celu zwiększenia odporności materiału w stanie nasyconym wodą na działanie mrozu oraz dla umożliwienia wykonywania dużych elementów, wprowadzono do składu masy drobne trociny drzewne i żużel paleniskowy.
Podany skład jest odpowiedni przy żużlu paleniskowym o ciężarze nasypowym około 750 kG/m3. Ze względu na płynną konsystencję masy surowej elementy autoklawizuje się w stalowych formach. Warunki autoklawizacji są podobne jak przy mikroporycie.
Gotowe elementy mają następujące właściwości.
Ciężar objętościowy
Ciężar objętościowy waha się od 1100 do 1250 kG/m3, zależnie od ciężaru nasypowego stosowanego żużla (program egzamin ustny). Wilgotność bezpośrednio po wykonaniu wynosi 10-15% wagowo. Wytrzymałość na ściskanie w stanie suchym zależnie od ciężaru objętościowego waha się w granicach 100-140 kG/cm2, w stanie nasycenia wodą od 80 do 115 kG/cm2. Wytrzymałość blokowa oznaczona na blokach o powierzchni 30 X 49 cm i wysokości 24 cm w kierunku prostopadłym do kierunku odlewania, w stanie powietrzno suchym wynosi 80-120 kG/cm2. Przyczepność do zbrojenia (orientacyjna) w stanie powietrzno suchym wynosi około 14 kG/cm2. Nasiąkliwość w procentach wagowych wynosi 38-P42%. Wilgotność sorpcyjna, przy wilgotności względnej powietrza cp = 60%, wynosi około 4%. Współczynnik sprężystości waha się w granicach 43000-7-63000 kG/cm2.
Wysokość kapilarnego podciągania w ciągu 48 godzin nie przekracza 5 cm. Odporność na działanie mrozu w stanie całkowitego nasycenia wodą zależy od struktury użytego żużla. Przy żużlu przepalonym o strukturze porowatej wyroby po 10 cyklach zamrażania ulegają nieznacznym uszkodzeniom. Ubytek na ciężarze wynosi poniżej 5%, a wytrzymałość na ściskanie zmniejsza się o mniej niż 10% (opinie o programie). Przy zawilgoceniu wynoszącym 50% w stosunku do nasiąkliwości beton jest odporny na działanie mrozu.
Cegłę wapienno-piaskową (inaczej wapienno-krzemowa lub silikatowa) otrzymuje się z mieszaniny piasku kwarcowego i wapna przez formowanie pod ciśnieniem w podwyższonej temperaturze.
Istotną cechą odróżniającą tworzywo cegły wapienno-piaskowej od zwykłej stwardniałej z biegiem czasu zaprawy wapiennej jest jego silne spojenie wskutek zachodzącej reakcji chemicznej między wapnem i ziarnami piasku. Mianowicie pod działaniem pary wodnej o zwiększonym ciśnieniu , około 4-7% krzemionki łączy się z wapnem tworząc nierozpuszczalne krzemiany wapnia. Nowo powstałe związki łączą ziarna piasku, zwiększając wytrzymałość wyrobów. Z biegiem czasu powstaje ponadto węglan wapnia, wskutek czego następuje dalszy wzrost wytrzymałości cegieł (segregator aktów prawnych).
powyższe, zaobserwowane w latach siedemdziesiątych ubiegłego stulecia, doprowadziły w roku 1880 do ustalenia przez Michaelisa sposobu produkcji cegły wapienno-krzemowej na skalę przemysłową. Od tego czasu powstało bardzo wiele odmian i ulepszeń w metodach fabrykacji. Produkcja rozwinęła się tak znacznie, że obecnie w niektórych krajach przewyższa produkcję cegieł wypalanych z gliny.
Zalety produkcyjne cegieł wapienno-krzemowych są następujące:
a) szybkość procesu fabrykacji - rozdrabnianie, mieszanie, formowanie i wyparzanie można przeprowadzać w ciągu 24 godzin;
b) małe zużycie spoiwa 6,5 do 12% wapna palonego w stosunku do ciężaru suchej mieszaniny wapna i piasku, tj. około 250-480 kG wapna na 1000 cegieł,
c) niewielkie zużycie paliwa - ok. IOO-T-175 kg węgla na 1000 sztuk;
d) możność produkowania cegły w miejscowościach, gdzie nie ma gliny, lecz można znaleźć piasek (promocja 3 w 1).
Koszt wyprodukowania cegły wapienno-krzemowej jest na pewno mniejszy niż koszt cegieł wypalanych z gliny, pod warunkiem że w pobliżu wytwórni znajduje się odpowiedni piasek oraz wapienniki.
Najnowsze wpisy
W ostatnich latach rozwój sztucznej inteligencji (SI) gwałtownie przyspieszył, wkraczając niemal w każdą dziedzinę naszej codzienności. Nie inaczej jest w…
Rosnąca potrzeba przyspieszenia procesów budowlanych, ograniczenia kosztów i minimalizacji negatywnego wpływu branży na środowisko sprawia, że innowacyjne technologie przyciągają coraz…
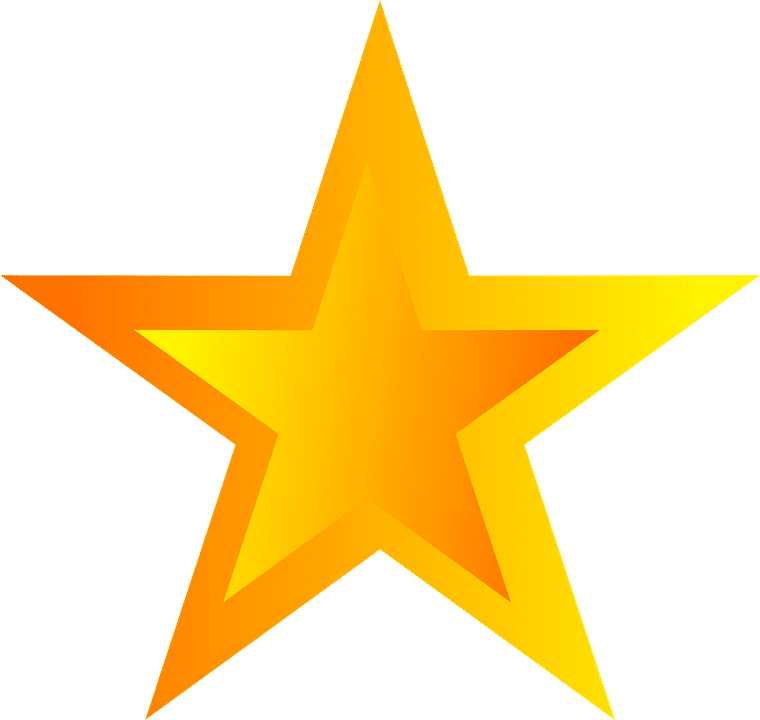
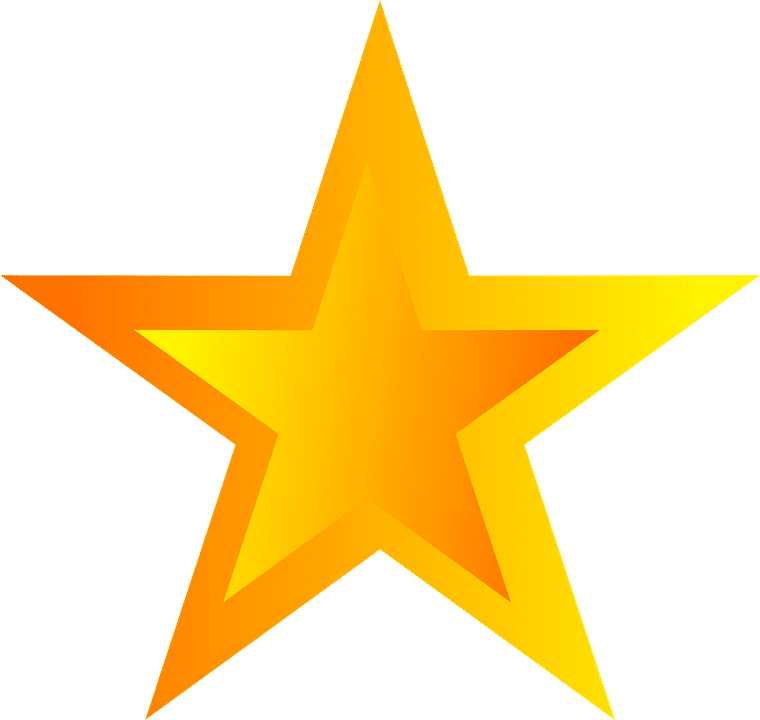
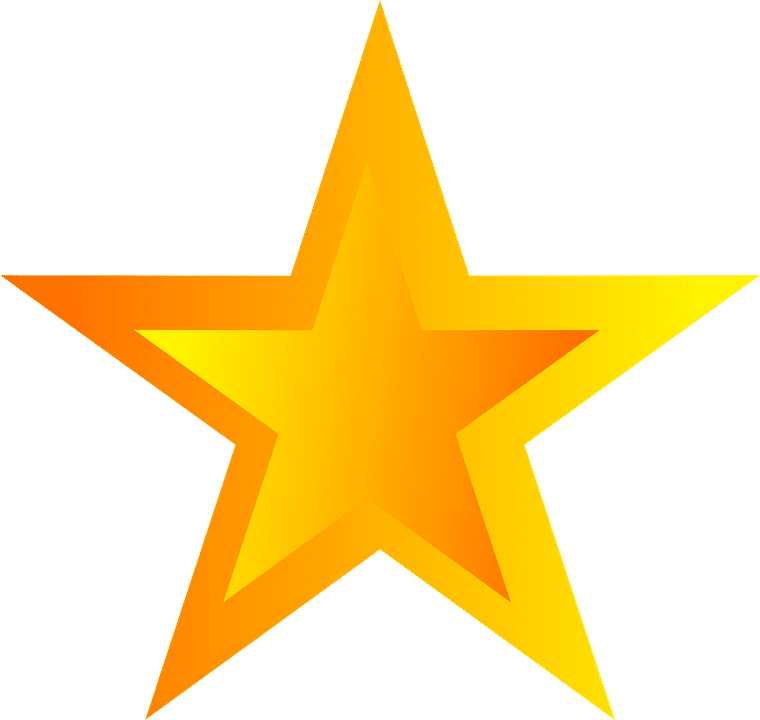
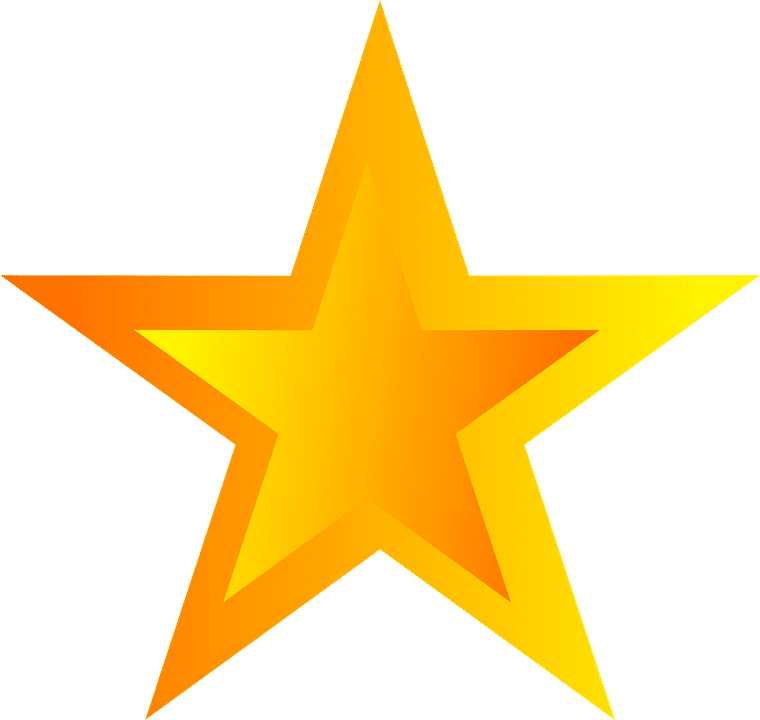
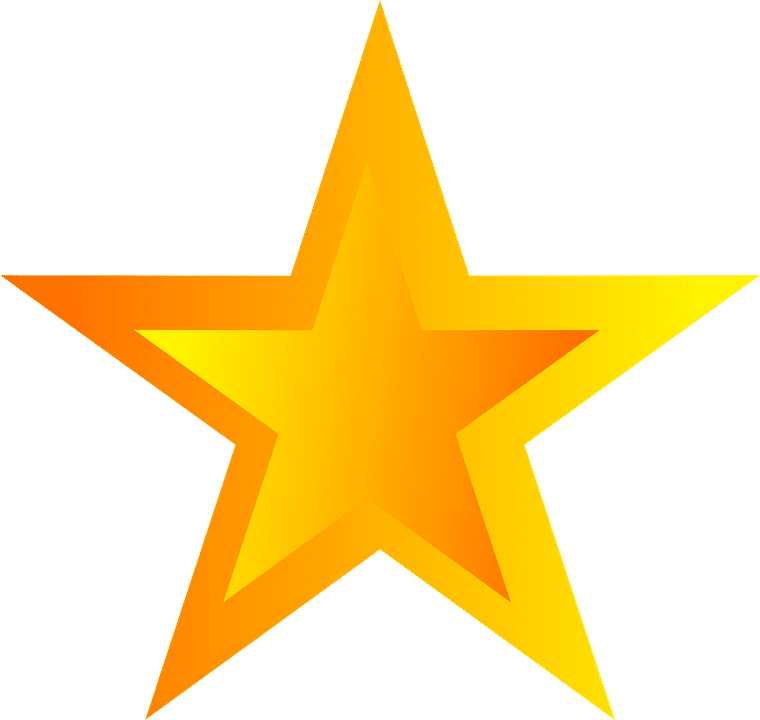
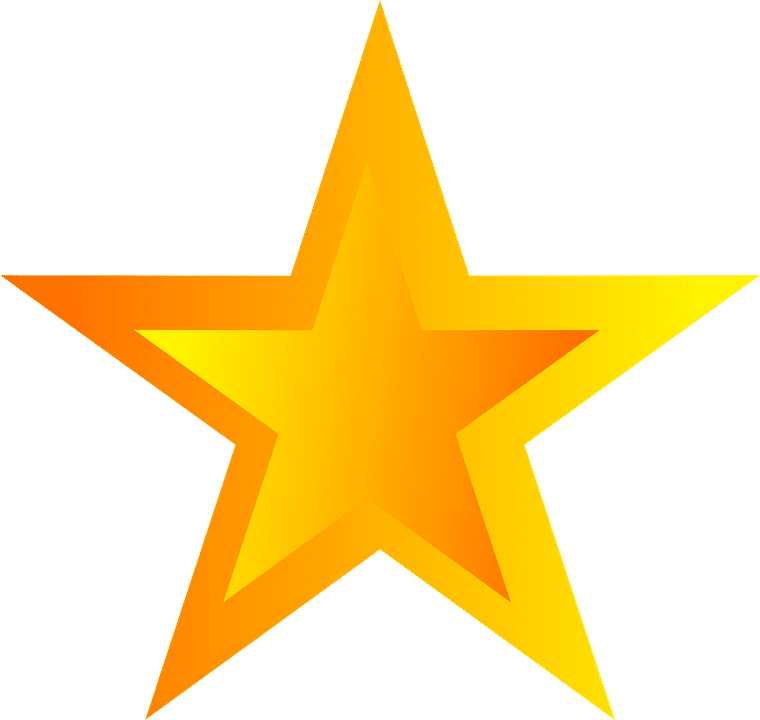
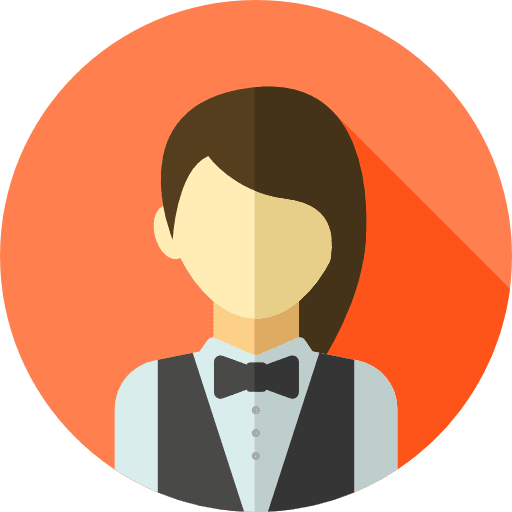
53 465
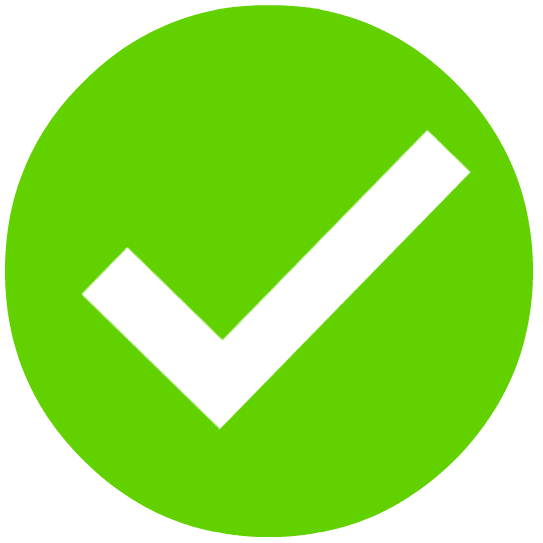
98%
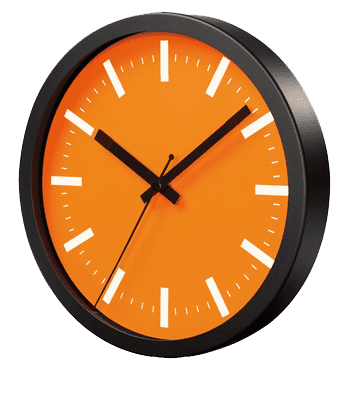
32