Blog

Wilgotność masy sypkiej
W artykule znajdziesz:

Szamot kordierytowy przygotowuje się przez spiekanie 80% gliny łatnieńskiej ŁT-1 i 20% magnezytu. Technologia przygotowania płyty kordierytowej jest dość trudna, ponieważ zakres temperatury spiekania jest wąski (program uprawnienia budowlane na komputer). Dlatego celowe jest scentralizowane wytwarzanie takich płyt i udoskonalenie zestawów surowcowych przez wprowadzenie np. wollastonitu do masy, wykorzystanie spoiwa fosforowego itp.
Skład materiału szamotowej płyty podkładowej leningradzkiego zjednoczenia produkcyjnego „Pobieda” jest, wg Kaca, następujący: 35,8% kaolinu, 53% szamotu ze złomu z osłon, 7% talku, 4,2% gliny czasowiarskiej. Wilgotność masy sypkiej powinna osiągać 8-12%. Produkuje się płyty o wymiarach 260x260x20 mm przez wytłaczanie pod ciśnieniem 5,5-6,0 MPa (55d-60 kG/cm2). Mają one nasiąkliwość 19%, porowatość 34%, wytrzymałość na zginanie 7,5 MPa (75 kG/cm2), współczynnik rozszerzalności cieplnej 6- JO-6, rotację 4-6 cykli. Czas tworzenia się czerepu na płycie podkładowej jest przykładowo taki: warstwa rozdzielająca - 0,5 min, warstwa podstawowa - 3-4 min, szkliwo - 2d-4 min (program uprawnienia budowlane na ANDROID).
Odpowietrzanie przez płytę podkładową, stosowane przez francuskich ceramików, przyspiesza tworzenie się czerepu, zmniejszając odpowiednio długość całego przenośnika. Przenośnik. Ciągły, zautomatyzowany proces odlewania płytek składa się z kilku operacji, które zachodzą przy kolejnym posuwaniu się płyt podkładowych na przenośniku (uprawnienia budowlane).
Płyta przechodzi pod zbiorniczkami maszyn natryskowych. Masa lejna ze zbiornika-mieszalnika, tłoczona pompą CM-938, przechodzi przewodem rurowym przez sito wibracyjne i w sposób ciągły równomiernie zalewa płytę; nadmiar masy lejnej ścieka do zbiorników pod przenośnikiem i wraca do produkcji. Przenośnik składa się z kilku odcinków, szybkość regulowana jest w granicach każdego odcinka. Zbiorniczki rozmieszczone są w następującej kolejności:
1) wylewanie warstwy rozdzielającej,
2) wylewanie podstawowej masy płytki,
3) wylewanie szkliwa.
Może być również wbudowany zbiorniczek do wylewania angoby. Odległości między zbiorniczkami są ustalone (program egzamin ustny).
Procesy suszenia
Po naniesieniu szkliwa surowego i zaniknięciu lustra wilgoci odlaną płytę rozcina się automatycznie nożami tarczowymi na podłużne pasy, następnie płyta podkładowa obraca się o 90° i cięcie powtarza się. Powierzchnię rozciętych płytek czyści się przez odmuchiwanie. Czoła płyt podkładowych czyści się tarczami, którymi ścina się nacieki szkliwa. Odwrotną stronę płyty podkładowej można oczyścić obracającymi się szczotkami z kordu lub na mokro (co jest niekorzystne ze względu na stopniowe zmniejszanie się nasiąkliwości) (opinie o programie).
Procesy suszenia i wypalania płytek na płytach podkładowych następują kolejno: stosowane są w tym celu piece szczelinowe z przenośnikiem rolkowym. Ciągi odlewnicze dla płytek o wymiarach 260x 260x 40 mm, wytwarzanych na podkładach, są zainstalowane w wielu wytwórniach. Wydajność każdego przenośnika wynosi 200 tys. m2 rocznie, liczba podkładów na szerokości przenośnika - 3, czas suszenia 11 min, temperatura suszenia - 300°C, czas wypalania i studzenia - 30 min, temperatura wypalania-1020°C. Wymiary podkładu wynoszą 200 x 200 x x 20 mm. Personel obsługi składa się z 15 ludzi (segregator aktów prawnych).
Problem rentowności pieców rolkowych i siatkowych do wypalania płytek odlewanych nie został jeszcze rozwiązany; za granicą stosuje się nawet piece z trzonem kroczącym. Płytki prasowane „mozaika”. Płytki „mozaika” wytwarzane są przeważnie metodą półsuchego prasowania, zgodnie z omówioną wyżej technologią. Wydajność linii opracowanych w Nllstrojkieramika wynosi 100, 200 i 350 tys. m2 rocznie. Linia potokowa obliczona na produkcję 100 tys. m2 mieści na szerokości przenośnika 12 szt. sprasowanych płytek. Prędkość przesuwania się przenośnika wynosi 0,5 m/min (promocja 3 w 1). Czas suszenia na trzonie siatkowym - 15 min w temperaturze 300°C. Czas wypalania gazem - 40 min w temperaturze 1000°C. Zużycie gazu - do 85 m3/h. Ogólne wydzielenie ciepła na zewnątrz wynosi 344,8 MJ/h (82,3 tys. kcal/h). Zużycie mocy do napędu - 25,8 kW. Linia ma 38,1 m długości, 43,2 m szerokości i 3 m wysokości. Linię obsługuje 4 ludzi.
Najnowsze wpisy
W ostatnich latach rozwój sztucznej inteligencji (SI) gwałtownie przyspieszył, wkraczając niemal w każdą dziedzinę naszej codzienności. Nie inaczej jest w…
Rosnąca potrzeba przyspieszenia procesów budowlanych, ograniczenia kosztów i minimalizacji negatywnego wpływu branży na środowisko sprawia, że innowacyjne technologie przyciągają coraz…
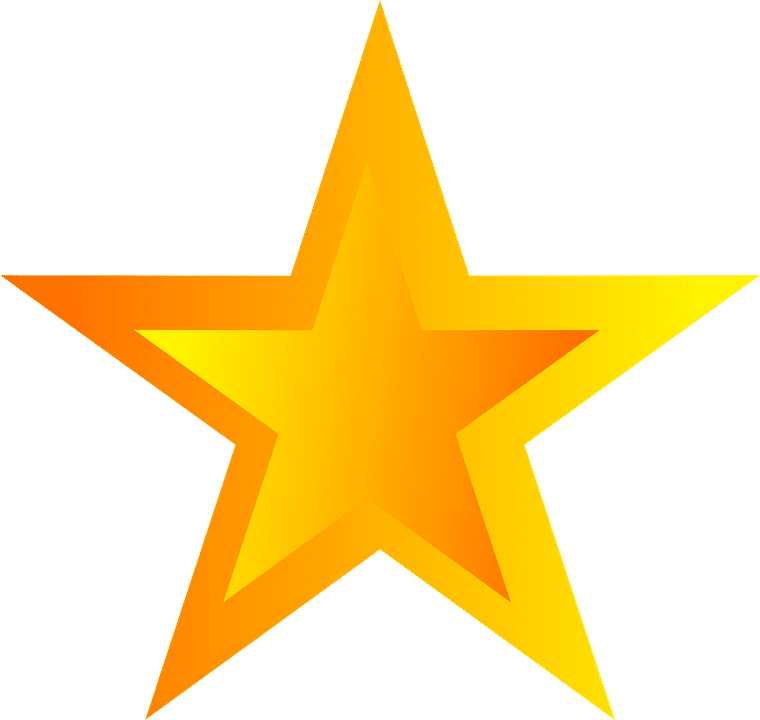
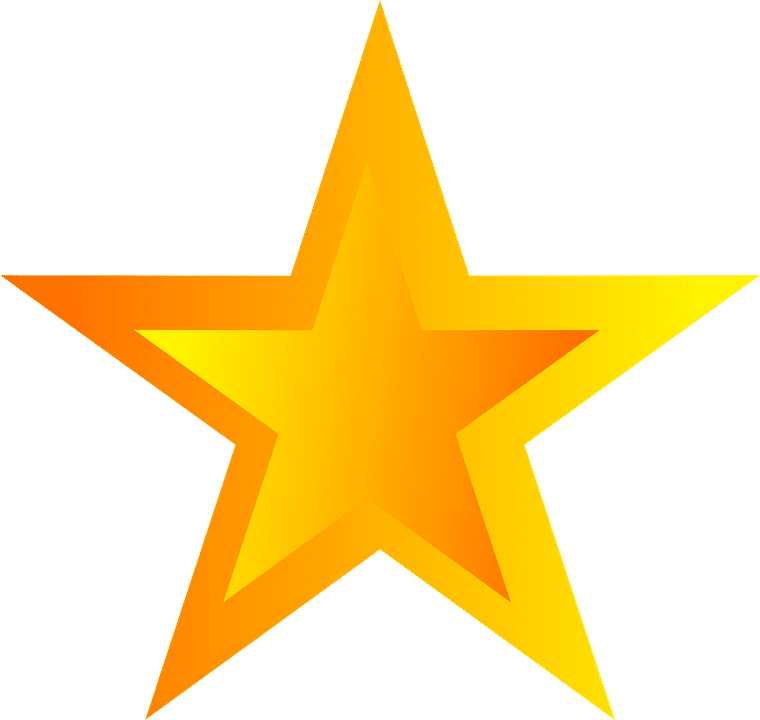
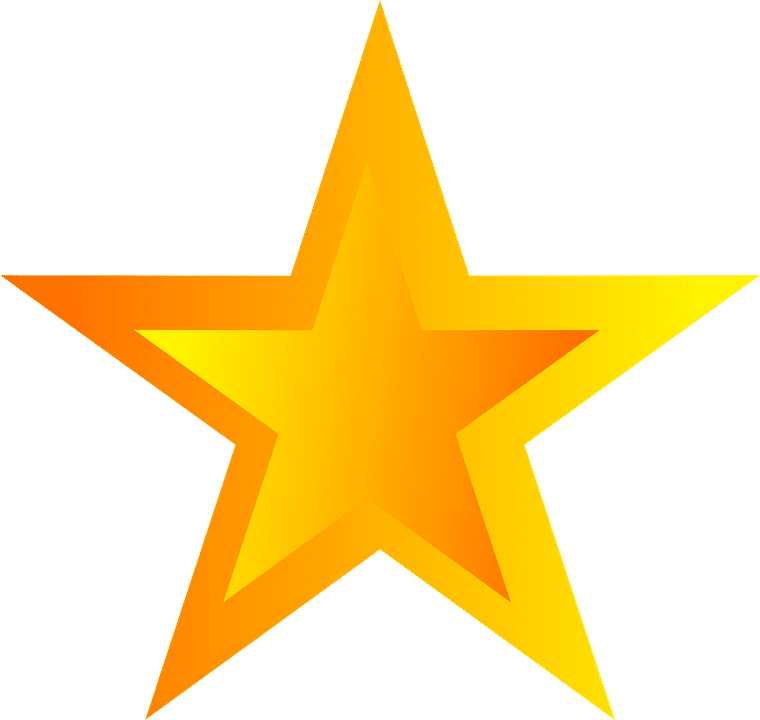
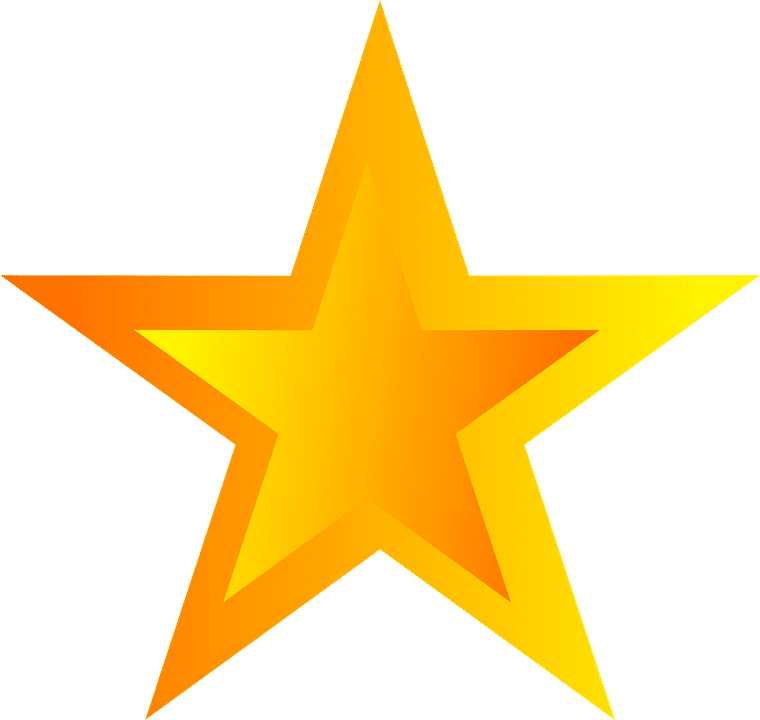
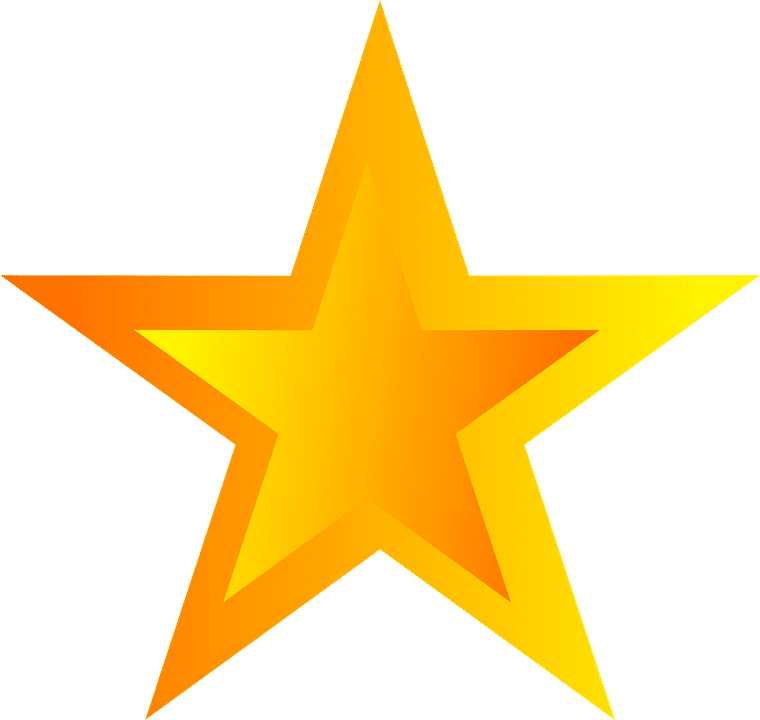
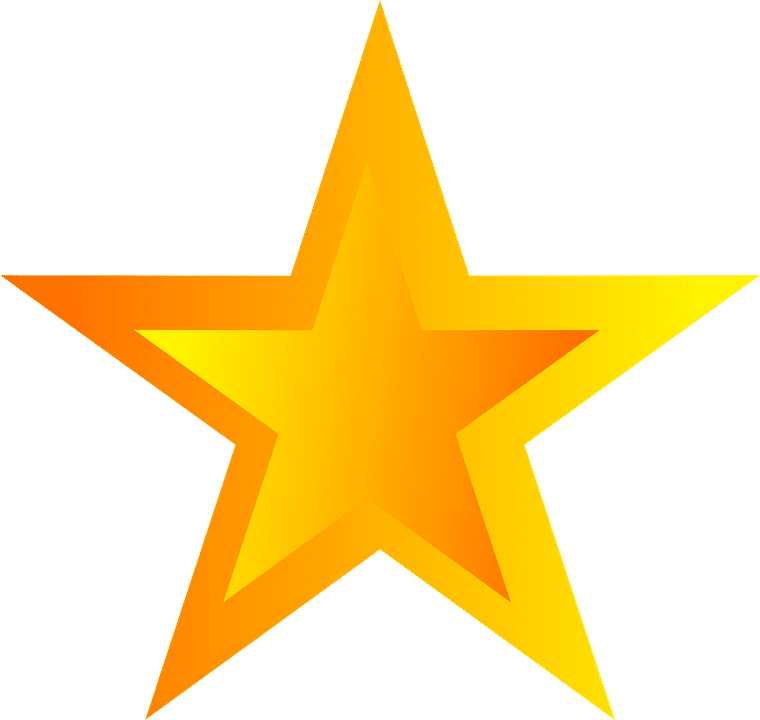
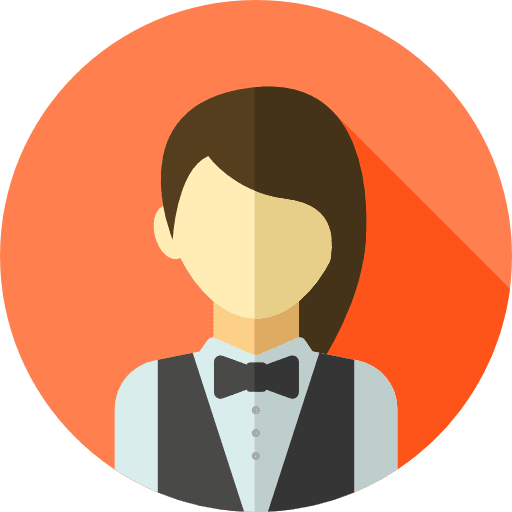
53 465
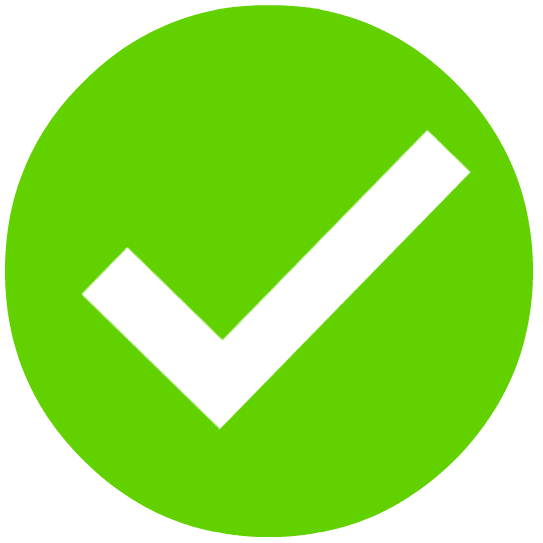
98%
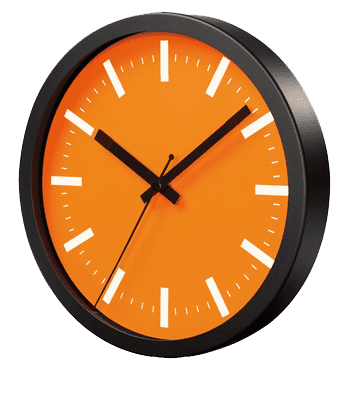
32