Blog

Powłoki metalowe
W artykule znajdziesz:

W zależności od sposobu nanoszenia ochronnych powłok metalowych można je podzielić na następujące rodzaje:
- powłoki elektrolityczne (galwaniczne) wytworzone na powierzchni zabezpieczanego metalu metodą elektrolityczną,
- powłoki metalizacyjne otrzymane na powierzchni metalu metodą metalizacji natryskowej,
- powłoki zanurzeniowe (ogniowe) otrzymane przez zanurzenie metalu chronionego w roztopionym metalu chroniącym (program uprawnienia budowlane na komputer),
- powłoki platerowane otrzymane metodą jednoczesnego działania podwyższonej temperatury i obróbki plastycznej, przy czym następuje ścisłe połączenie między metalem powłoki i metalem chronionym (np. walcowanie na gorąco),
- powłoki kontaktowe otrzymane przez redukcję metalu bez stosowania zewnętrznego źródła prądu (program uprawnienia budowlane na ANDROID).
Powłoki metalowe dzielą się na anodowe i katodowe. Metal powłok anodowych ma potencjał bardziej ujemny od potencjału metalu chronionego. Nie muszą to być powłoki ścisłe, przy obecności elektrolitu w powstającym ogniwie korozyjnym metal podłoża będzie spolaryzowany katodowo i będzie chroniony elektrochemicznie przez rozpuszczanie się metalu powłoki ochronnej. Powłoki te nie odznaczają się więc dużą trwałością i nie mogą być stosowane w agresywnych warunkach korozyjnych. Do powłok anodowych należą np. powłoki cynkowe lub kadmowe na żelazie (uprawnienia budowlane).
Jeżeli metal powłoki ochronnej ma potencjał bardziej dodatni od metalu chronionego, to taka powłoka nazywa się katodową, a skuteczność jej działania w decydującym stopniu zależy od ścisłości i szczelności, czyli niedopuszczania środowiska korozyjnego do metalu podłoża, inaczej bowiem będzie w miejscach uszkodzeń powłoki następować intensywna korozja. Do powłok katodowych należą powłoki z miedzi, niklu lub chromu na żelazie.
Powłoki galwaniczne mają wiele zalet w porównaniu z innymi powłokami metalowymi, przede wszystkim można tu właściwie dowolnie regulować grubość warstwy ochronnej, natomiast sama warstwa wykazuje dość dużą porowatość. Do najczęściej stosowanych powłok galwanicznych należą powłoki cynkowe, skutecznie chroniące konstrukcje przed korozją atmosferyczną: bardzo często stosuje się je do ochrony różnego rodzaju rur i zbiorników (program egzamin ustny).
Powłoki metalizacyjne
Powłoki metalizacyjne są stosowane również do ochrony tworzyw niemetalowych, np. drewna, betonu, wyrobów ceramicznych, materiałów budowlanych itp. Bardzo często stosuje się powłoki dwuwarstwowe, gdzie metal warstwy ochronnej umieszcza się na specjalnej warstwie podkładowej. Zasadniczą wadą powłok metalizacyjnych jest ich duża porowatość, zanikająca dopiero po uzyskaniu dość dużej grubości. Często stosuje się więc powłoki wielowarstwowe, z kilku warstw tego samego metalu (opinie o programie).
Do bardziej rozpowszechnionych powłok metalizacyjnych dla stali należą powłoki anodowe cynkowe i aluminiowe, stosowane dla zabezpieczenia konstrukcji przed korozją atmosferyczną i przed działaniem wody. Powłoki aluminiowe chronią ponadto stal przed działaniem wysokich temperatur (segregator aktów prawnych).
Powłoki zanurzeniowe są stosowane przede wszystkim do gotowych wyrobów lub ich części, np. różnego rodzaju armatury i osprzętu instalacyjnego. Do ochrony stali stosuje się głównie powłoki cynkowe uzyskiwane przez zanurzenie żelaza (temperatura topnienia 419°C) w roztopionym cynku (temperatura topnienia 327°C), powłoki cynowe oraz ołowiane. Wadą powłok zanurzeniowych jest duże zużycie drogich metali (cynk) i nierów- nomierność pokrycia przy dużej jego grubości.
Powłoki platerowane są stosowane tylko do wyrobów specjalnych, np. aparatury chemicznej wykonanej z tworzyw o małej odporności korozyjnej. Dotyczy to np. aparatury wykonanej ze zwykłej stali, pokrywanej wykładziną ze stali chromoniklowej niklu, tytanu lub tantalu (promocja 3 w 1). Ochronne powłoki kontaktowe (niklowe) uzyskuje się przez redukcję soli niklu np. tiosiarczanem sodowym w temperaturze rzędu 90 C. Na powierzchni metalu (takiego, który katalitycznie przyspiesza przebieg redukcji niklu, np. żelazo-nikiel, aluminium) powstaje równomierny osad, a po wygrzaniu w temperaturze ponad 400 C na powierzchni tworzy się stop z roztworu niklu i Ni3P o grubości 25-30 pm i praktycznie bez porów.
Najnowsze wpisy
W ostatnich latach rozwój sztucznej inteligencji (SI) gwałtownie przyspieszył, wkraczając niemal w każdą dziedzinę naszej codzienności. Nie inaczej jest w…
Rosnąca potrzeba przyspieszenia procesów budowlanych, ograniczenia kosztów i minimalizacji negatywnego wpływu branży na środowisko sprawia, że innowacyjne technologie przyciągają coraz…
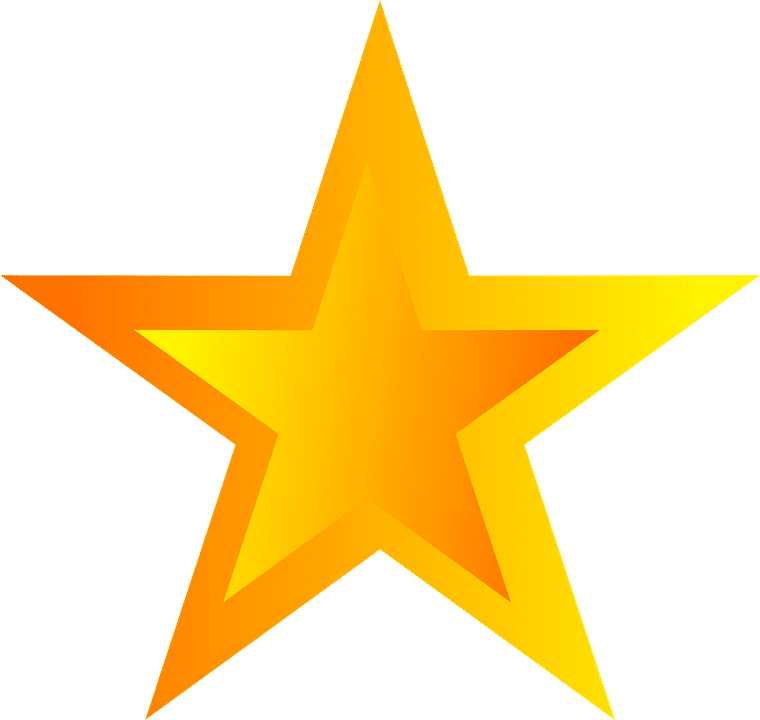
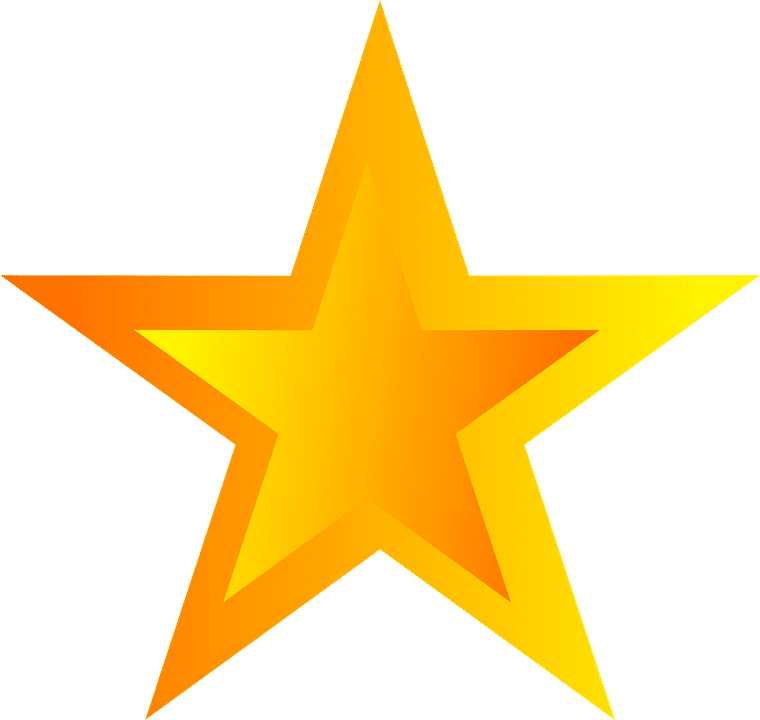
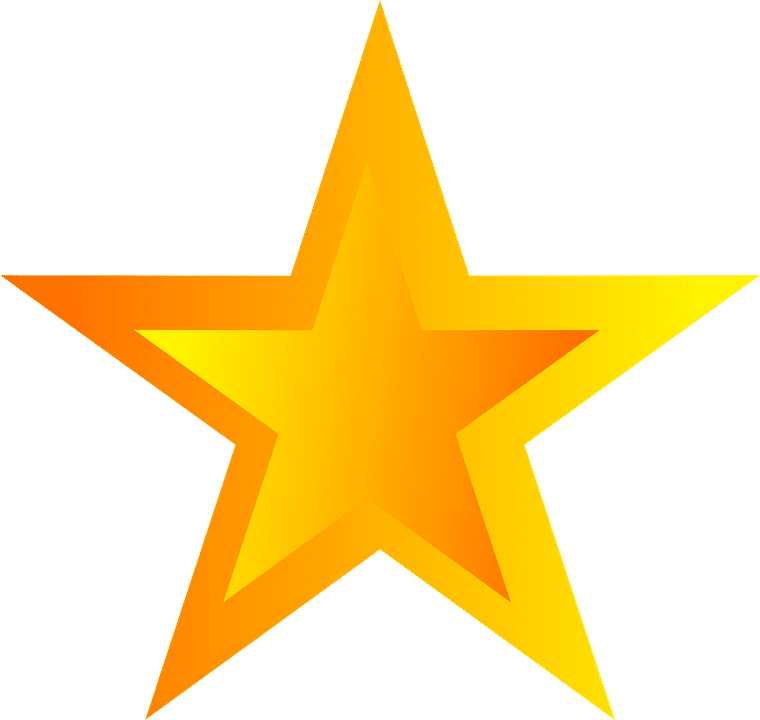
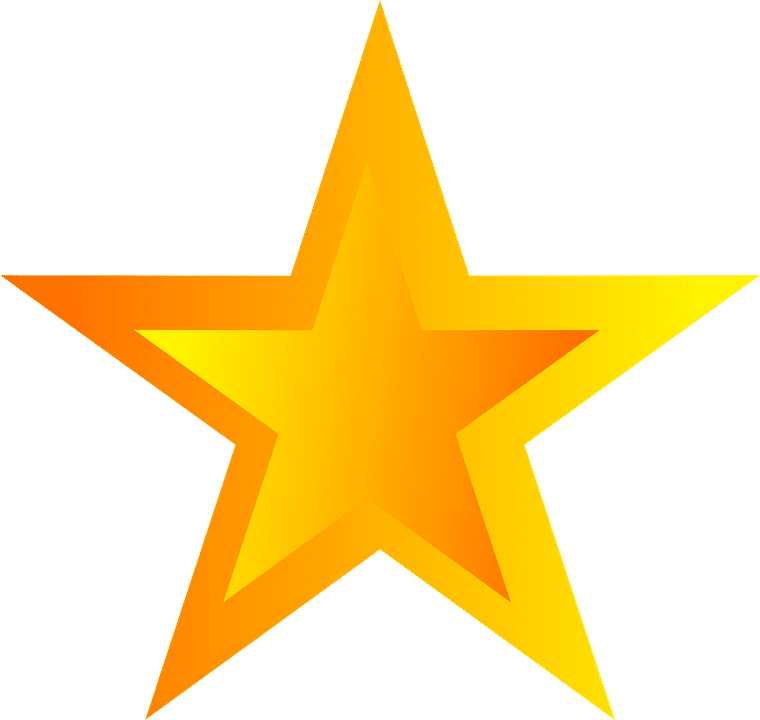
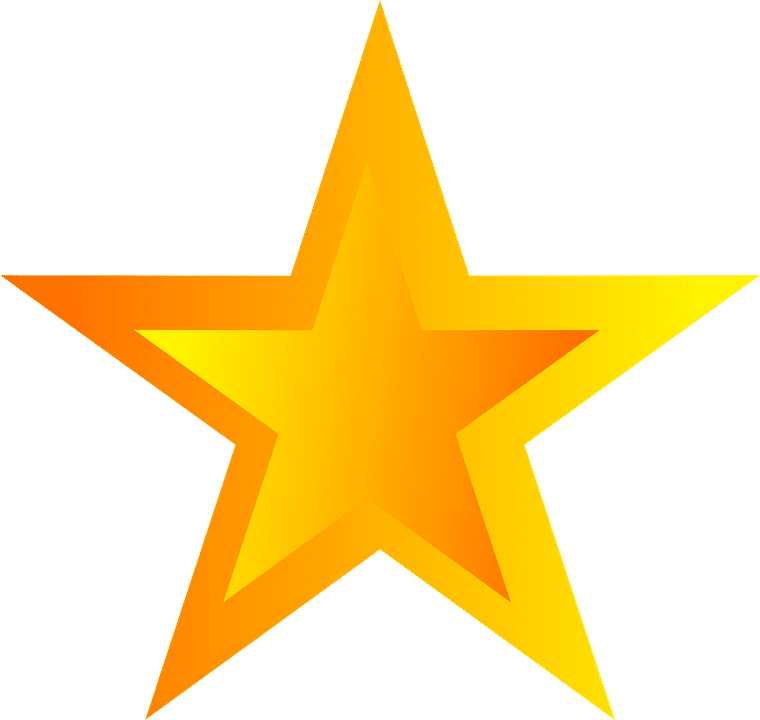
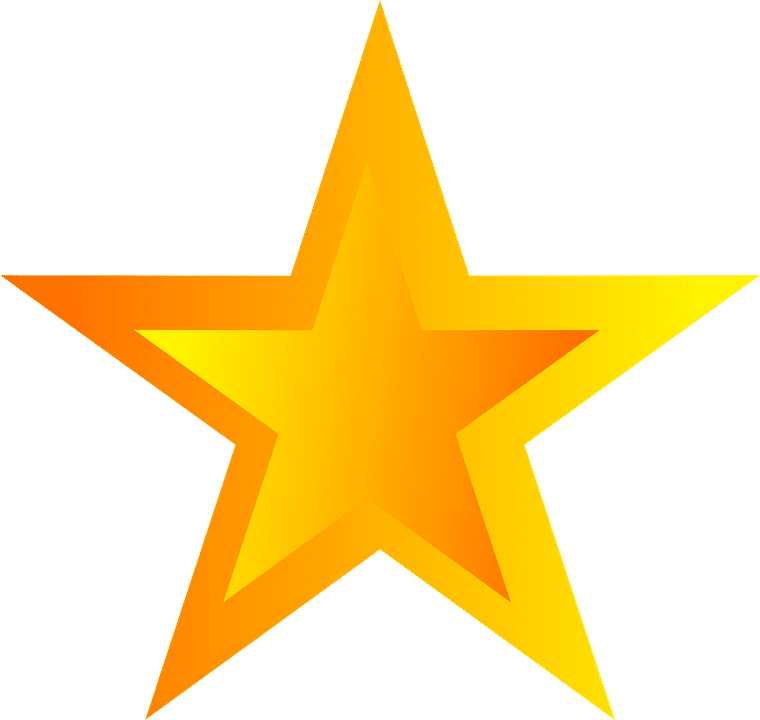
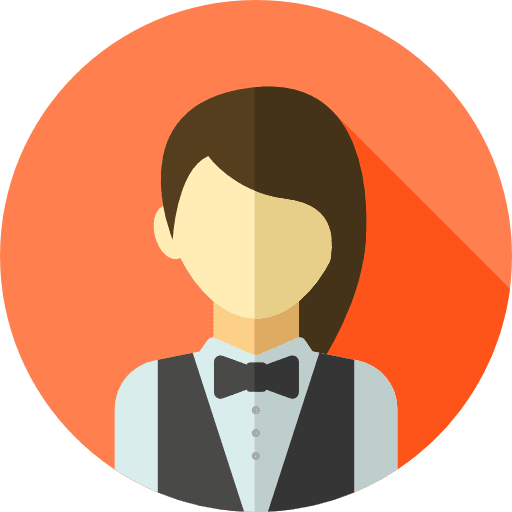
53 465
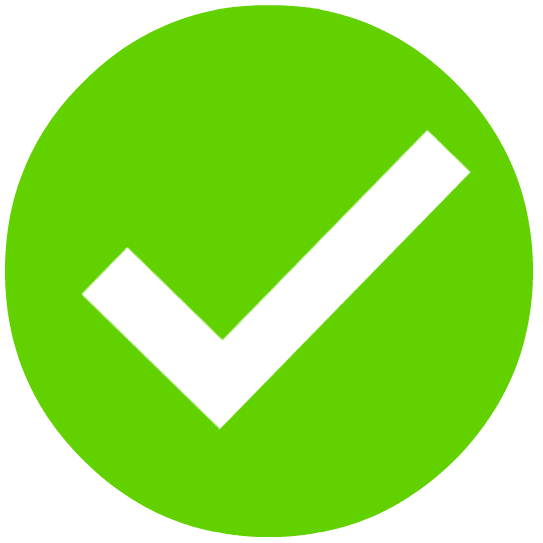
98%
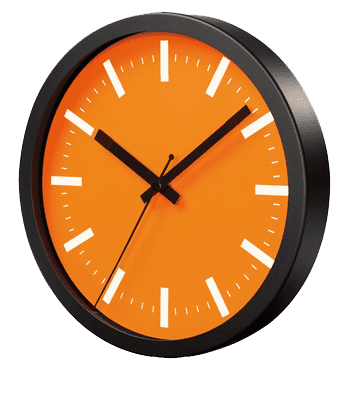
32